Environmental Management
16 minWe seek to reduce the environmental impact of our production and to adhere to environmental laws and regulations.
Why it matters
Every business, government, and individual has a role to play in meeting the goals of the Paris Agreement. For our part, dormakaba aims to reduce our energy consumption and related emissions. We use the latest scientific knowledge to guide a sound management approach. Our energy-intensive processes include melting, and aluminum and zinc die casting. We use these materials to manufacture numerous products, including hotel and high-security locks, door closers, fittings, and door handles.
Find out how we acquired an ISO matrix certification to improve our environmental management processes.
Read storyKey activities
We seek to reduce the environmental impact of our production and to adhere to environmental laws and regulations. We focus on improving our management of environmentally related processes and on monitoring and reducing our energy consumption, carbon emissions, water consumption, and effluents, as well as monitoring our waste disposal and recycling rates.
Environmental management is embedded at both the Group and local levels of our various production sites. Several sites have environmental officers, while others have incorporated environmental management into their quality assurance processes.
Our environmental management covers the following aspects:
- Energy and emissions
- Water and effluents
- Waste
Energy and emissions
The emission of greenhouse gases, which are generated through the use of fossil fuels, is one of today’s biggest challenges. In 2018, we committed to setting science-based targets and to having these validated by the Science Based Targets initiative (SBTi).
We are the first within the access solutions industry to have emissions targets approved by the Science Based Target initiative
In 2021, SBTi has approved our targets for operational and value chain emissions, including emissions from purchased materials and the use of our products. We are the first in the industry to have targets validated by the SBTi. Progress against the operational emissions target is being tracked as part of our sustainability-linked credit facility. The targets will be announced publicly as we unveil our new corporate strategy by the end of the calendar year.
As a further commitment, we have set an interim carbon emissions reduction target of –5% tonnes of carbon dioxide equivalent (tCO2e) by the end of the financial year 2020/21 for the reporting scope and baseline of the financial year 2017/18. We are pleased to report that we have exceeded this target level. We reduced 20% versus the baseline, with approximately 17 percentage points stemming from increased purchase of renewable energy and energy efficiency projects. Other reductions in emissions are explained by decreased production due to the business impact of Covid-19 particularly in the financial year 2019/20, consolidation of production facilities in the USA, improvements in data quality and changes in seasonal weather patterns.
Energy consumption
Total energy consumption was over 250,000 MWh in the financial year 2020/21. Electricity and fuels for heating or manufacturing both play a crucial role in our production processes, constituting nearly 80% of total energy consumption. The remainder is associated with the fuel consumption of our vehicle fleet.
Many components used to create our products are manufactured in-house, and purchased parts require further processing, both of which impact total energy demand. As a result, we focus many of our energy saving initiatives in this area.
In the financial year 2020/21, energy saving initiatives were being implemented at various sites in the reporting coverage. This work included retrofitting facilities to LED lighting and automated control systems; upgrading equipment such as air compressors and an air dryer; the optimization of heating and cooling systems; and the procurement as well as on-site production of renewable electricity.
As a result, we realized total quantifiable annual energy savings of approximately 2,900 MWh for the sites covered in the scope of this report. In addition, over 58,000 MWh (45.5%) of the electricity that we consumed came from renewable sources. In our Access Solutions (AS) EMEA segment, this share already reached over 80%. All other segments showed a percentage of electricity consumption from renewable resources ranging from 34% to 60%.
45.5% of our purchased electricity came from renewable sources
Examples of energy reduction activities in the financial year 2020/21 included:
- AS AMER at the Indianapolis (USA) manufacturing facility reduced natural gas usage by approximately 11,000 million BTU/year after replacing a 4 million BTU gas-fired space heater with a heating, ventilation, and air conditioning (HVAC) system. The Montreal (Canada) manufacturing site included LEED certification criteria in its building expansion project and the Reamstown (USA) facility switched to LED lightning. The Nogales (Mexico) manufacturing site installed a more efficient air compressor, implemented a lighting shutdown process, and started the conversion to LED lightning.
- AS APAC optimized the usage of air conditioners at the Chennai (India), Yantai and Shenzhen (China) sites. In addition, the Chennai facility completed the ISO 50001 recertification. The Taishan (China) manufacturing site has begun purchasing steam produced as a byproduct of industrial processes from a neighboring facility, thus eliminating the need to use a diesel boiler as had previously. These and other improvements resulted in annual energy savings of 5%.
- AS DACH at the Ennepetal (Germany) manufacturing site switches off the refrigeration system for several hours during weekends, resulting in energy savings of 29,120 kWh/year. In addition, the retrofit of LED lighting saved 22,080 kWh/year. At the Singapore manufacturing facility we achieved around 1.4% (223,000 kWh/year) reduction in energy consumption by optimizing the chiller and air handling unit system. Our manufacturing facilities in Suzhou (China), Melaka (Malaysia), and Singapore are now ISO 50001 certified.
- AS EMEA at the Fougéres (France) manufacturing facility changed its air dryers from desiccant to refrigerant technology, which decreases the electricity consumption of the compressor by 3.5% on an annual basis. At the Wetzikon (Switzerland) facility, a three-year energy efficiency project has been completed with the modernization of the heating, ventilation, and air conditioning (HVAC) system, which is to reduce heating oil consumption by 86,000 liters per year and carbon emissions by 288 tonnes per year.
in MWh |
| 2020/21 |
Energy consumption |
| 252,574 |
Electricity |
| 125,136 |
District heating |
| 1,627 |
Heating fuels total |
| 67,924 |
Heating oil and diesel for backup generators |
| 6,828 |
Natural gas |
| 59,334 |
LPG/propane |
| 1,763 |
Vehicle fuels total |
| 57,886 |
Diesel |
| 44,174 |
Gasoline |
| 11,809 |
LPG/propane |
| 1,766 |
Other vehicle fuels: bioethanol and natural gas |
| 138 |
Energy use
(MWh)
Purchased electricity by source
(%)
Energy intensity (MWh/mCHF net sales)
Energy use by segment (MWh)
Purchased electricity by segment (MWh) *
Percentage of purchased electricity from renewable sources by segment (%) *
Greenhouse gas emissions
In the financial year 2020/21, our total greenhouse gas emissions (GHG) amounted to around 70,000 tCO2e. Nearly 60% were emitted as a consequence of electricity consumption, followed by vehicle and heating fuel consumption, and volatile as well as process gas emissions. Climate-related initiatives implemented during the reporting year resulted in total annual savings of approximately 15,500 tCO2e (nearly 21% of our total footprint from own operations).
Our annual greenhouse gas emissions savings was 15,500 tCO2e
Due to the implementation of the energy-saving initiatives outlined above, we expect to reduce our annual GHG emissions by approximately 1,100 tCO2e. We also worked diligently to source renewable electricity or generate own renewable energy wherever feasible, leading to an annual emissions avoidance of approximately 14,400 tCO2e.
Examples of GHG reduction activities in the financial year 2020/21 included:
- Our AS EMEA facilities in Milan and Castel Maggiore (Italy) switched to green electricity, saving 66 tCO2e per year. The rollout of a fuel-efficient driving training across UK & Ireland has been completed, with in-cab feedback technology built in into about 100 vehicles; furthermore, electric vehicle charging points were installed.
- Key & Wall Solutions started a pilot project on e-mobility in Germany and expanded the solar panel installation in the Senai (Malaysia) manufacturing facility, resulting in an annual carbon emission reduction of 19.8%.
Greenhouse gas emissions by source
(tCO2e)
Scope 1 and Scope 2 emissions
(tCO2e)1
- Greenhouse gas inventory calculated in accordance with the WRI/WBCSD Greenhouse Gas Protocol. Emission factor sources: UK Defra (2019), US EPA eGRID (2018), IEA (2019), AIB (2018).
- Scope 1: direct greenhouse gas emissions from sources owned or controlled by dormakaba.
- Scope 2: indirect greenhouse gas emissions from sources owned or controlled by another entity, as a consequence of the company’s activities.
- Biogenic emissions associated with the combustion of biofuel amount to 20 tCO2e. These are called "outside of scope" emissions and reflect the impact of burning biomass and biofuels. The fuel source itself absorbs an equivalent amount of CO2 during the growth phase to that released through combustion).
- The greenhouse gas emissions associated with electricity consumption are reported according to the “market-based approach”, as defined in the Greenhouse Gas Protocol Scope 2 Guidance. When reported according to the “location-based approach”, the Scope 2 emissions totaled 60,370 tCO2e.
Greenhouse gas emissions by segment (tCO2e)
Carbon intensity
(t CO2e/mCHF net sales)
Year-on-year absolute Scope 1 and 2 emissions
(t CO2e)
As part of our commitment to the Science-Based Targets initiative, we carried out a screening and carbon inventory development of Scope 3 emissions in the financial year 2018/19 . The screening showed that the largest sources of Scope 3 emissions stem from purchased goods and services (75%) and use phase of sold products (11%). We also learned that Scope 3 emissions constituted around 90% of our combined Scope 1, 2 and 3 carbon emissions, highlighting the importance of Scope 3 emissions to our climate strategy. In a second phase, we therefore developed carbon inventories for these categories of purchased goods and services and use phase of products. For the latter, we calculated the footprint of the 334 products that consume energy after installation, including those that are battery-operated. For the financial year 2020/21, value chain emissions for the use phase of products totaled 181,600 tCO2e. As mentioned, value chain emissions from purchased goods and services represents the vast majority, totaling 802,400 tCO2e in the reporting period.
Scope 3 emissions: purchased goods and services
(tCO2e)
Scope 3 emissions: use phase of products
(tCO2e)3
- Calculated via direct material weight. Emission factor sources: UK Defra (2019), US EPA eGRID (2018), IEA (2019), AIB (2018).
- Calculated via spend volume.
- Calculated via energy consumption during the use phase. Emission factor sources: UK Defra (2019), US EPA eGRID (2018), IEA (2019), AIB (2018).
Water and effluents
In the financial year 2019/20, dormakaba reassessed the water stress levels for all our sites, including those beyond the regular scope of this report. The new analysis revealed that approximately 40% of sites have the potential for high to extreme water stress, defined as a “water demand to supply ratio of 40% or greater for the respective municipality”. The water stress analysis is based on the two databases Aqueduct Water Risk Atlas by the World Resources Institute and AQUASTAT by the Food and Agriculture Organization. Results of the updated risk assessment were shared with those sites having (1) high or extreme water stress, and (2) high water consumption relative to other sites for development of mitigation plans. Commitment to water stewardship initiatives and reduction targets for seven of these manufacturing sites have been agreed in the financial year 2020/21.
Water stress level by sites*
The majority of our total water consumption is municipal water used for cooling, manufacturing processes, and for sanitation purposes. Wastewater is mainly discharged via the local municipal sewerage system, in compliance with local requirements and treated by third-party companies where necessary.
Examples of contribution to water-saving activities and good practices in effluents management in the financial year 2020/21 included:
- AS AMER optimized the wastewater treatment process at the Indianapolis (USA) facility and achieved 50% increase in throughput and decreased the use of treatment chemicals. At the Huntsville (USA) manufacturing facility, the water used for washing parts was recirculated into the system, resulting in a significant reduction of approximately 50% in overall water usage for the site. At the Montreal (Canada) facility, 36% of the washing and urinal systems in washrooms are now touchless.
- AS APAC at the Chennai (India) facility installed an electromagnetic flow meter to quantify and control sewage discharge; furthermore, in the toilets and washroom areas the new control valve solutions resulted in the reduction of water consumption by 5% per year. At Taishan, the water consumption was reduced by 3% on a YoY basis by correcting leakages in the underground pipeline and by optimizing water consumption in the canteen.
- AS DACH at the Ennepetal facility replaced the gravel filter with a drum belt filter in the wastewater treatment plant of the electroplating unit, which resulted in lower zinc and iron levels in the wastewater; furthermore, they introduced a cobalt-free coating process for corrosion protection. At the Singapore and Suzhou (China) facilities, the water consumption trend is monitored, in line with the water stewardship effort, which allows the detection of unusual levels of consumption.
- Key & Wall Solutions at the Lima (Peru) manufacturing facility established a new wastewater treatment plant, which is expected to recycle up to 80% of the water usage. As the factory is not connected to the municipal water system, it will help to reduce water purchase by 70%.
Water consumption
(m3)
Wastewater discharge
(m3)
Water intensity
(m3/mCHF net sales)
Waste
Next to water consumption and effluents, waste management is of key importance during the electroplating, surface finishing, and painting processes. Our filter systems ensure that potentially hazardous substances are not released externally.
Toxic waste arising from painting and electroplating is disposed of as special waste. In addition, scraps from turning and milling or punching are recycled, and returned, for example, to the suppliers of the raw materials. Certified disposal companies are commissioned to dispose of industrial waste and chemicals, and to recycle materials.
The generation of different waste streams is an inevitable consequence of our operations. We monitor our waste by treatment method and waste type. Approximately 76% of the waste stream was recycled, reused, or recovered (including raw materials and energy recovery) in financial year 2021/21. At about 74% by weight, the largest proportion of waste is scrap metal.
Examples of contribution to waste activities in the financial year 2020/21 included:
- AS AMER implemented a program at the Nogales (Mexico) manufacturing facility to separate organic and inorganic waste in the cafeteria. The organic waste is now diverted to a local farm as animal feed and so the general garbage volume has been reduced by 26%.
- In Germany, AS DACH has continued recycling 96% of the waste in the production facility in Ennepetal (Germany).
- AS EMEA’s manufacturing facility in Konstancin-Jeziorna (Poland) introduced steps to reduce paper waste, for example through electronic document circulation, the reuse of cardboard boxes and fillers for shipments, and the use of electronic order forms.
Non-hazardous waste by type
(metric tons)
Waste by treatment path
(metric tons)
Hazardous waste by type
(metric tons)
Waste intensity
(t/mCHF net sales)
Our performance
To ensure our environmental management is state of the art, we refer to international standards for environmental management (ISO 14001) and energy management (ISO 50001). All manufacturing sites that have more than 100 employees, and use non-negligible amounts of hazardous materials, are expected to maintain an environmental management system based on ISO 14001. Those with production process that could potentially seriously harm the environment are required to certify their environmental management system. These processes include plating, anodizing, polishing, galvanizing, painting, and casting.
45% of all our manufacturing sites are ISO 14001 certified
Today, 50% of the manufacturing sites based on our baseline reporting scope in 2017/18 have achieved ISO 14001 (or similar) certification, which is in line with our strategic target on increasing coverage to this level by the end of the financial year 2020/21.
In the financial year 2020/21, 9 of our manufacturing sites in Germany (Villingen-Schwenningen, Velbert, Bad Berka), Austria (Herzogenburg, Eggenburg) and Switzerland (Wetzikon, Rümlang, St. Gallen, Lausanne), were ISO 14001 certified and handle environmental issues according to the international standard.
Further, all manufacturing plants are expected to maintain an energy management system based on ISO 50001 by the end of the financial year 2021/22. Smaller manufacturing sites (e.g., local assembly centers) have been given an extended deadline for achieving this until the end of the financial year 2022/23. Currently, 21% of manufacturing sites have met this standard. In order to raise awareness and clarify expectations, a checklist on Group standards for energy management systems was developed and shared with all manufacturing sites.
Segment |
| ISO 14001 Certificate |
| Maintain Environmental Management System |
| ISO 50001 Certificate |
| Maintain Energy Management System |
AS AMER |
| 2 |
| 13 |
|
|
| 3 |
AS APAC |
| 3 |
| 5 |
| 1 |
| 5 |
AS DACH |
| 8 |
| 9 |
| 5 |
| 7 |
AS EMEA |
| 14 |
| 17 |
|
|
| 5 |
KWS |
| 6 |
| 8 |
| 1 |
| 3 |
Total |
| 33 |
| 52 |
| 7 |
| 23 |
% locations covered in reporting scope* |
| 32% |
| 51% |
| 7% |
| 23% |
% employees covered (based on FTEs) |
| 62% |
| 72% |
| 19% |
| 43% |
*Including offices
There have been no incidents of non-compliance with environmental laws or regulations in the financial year 2020/21.
Outlook
We will continue our efforts to achieve our target towards full coverage of manufacturing sites with energy management systems and to advance our global environmental activities. Planned projects and initiatives include:
- AS AMER will implement energy management systems at all manufacturing sites; furthermore, it plans energy performance evaluations for the Indianapolis (USA) and Montreal (Canada) facilities. The Huntsville (USA) facility plans to evaluate the current chemicals used to clean parts in the wash system. This initiative will allow the facility to convert to a non-hazardous, alkaline cleaner and sealer that will only produce small volumes of landfillable waste, and no byproducts requiring removal of hazardous waste.
- AS APAC in the Chiayi (Taiwan) facility is planning to install a rooftop solar panel system.
- AS DACH plans the conversion to LED lighting at the Bad Salzuflen (Germany) site, which is expected to result in annual energy savings of 186,278 kWh. In Melaka (Malaysia), we plan to purchase green electricity, aiming to reduce emissions by 2835 CO2e. The segment also plans to gain ISO 14001 certification at 3 locations in Germany (Bad Salzuflen, Bühl, and Zusmarshausen).
- AS EMEA at the Fougéres (France) facility will refurbish the heating and ventilation system, while in Konstancin-Jeziorna (Poland) and Wetzikon (Switzerland) LED lights and motion detectors will be installed.
- Key & Wall Solutions expects to implement ISO 50001 and ISO 45001 management systems across 9 sites and three ISO 14001 certifications across various facilities.
Improving environmental management processes through matrix certification
During the financial year 2020/21, nine of our operational sites in Germany, Austria, and Switzerland became ISO 9001, ISO 14001, and ISO 45001 certified under one coordinated audit process. As a result, we have achieved a matrix certification, which simplifies processes between the countries and saves audit costs and time, while also increasing customer satisfaction.
ISO 14001, the most widely used international standard for environmental management systems (EMS), helps to better manage and control environmental processes, reduce negative impacts, and ensure legal compliance. ISO 14001 is accompanied by ISO 45001, which additionally covers topics related to occupational health & safety, and ISO 9001, which is concerend with quality management.
In the first year of the certification process the focus was, among others things, on the implementation of environmental management processes, reporting, measurement, REACH and RoHS regulations, as well as business continuity management, including risk analysis and crisis action plans.
Despite the Covid-19 situation, which added even more challenges to this generally complex audit process, we have successfully reached our goal. The dedicated and professional work of the Quality Managers and other team members, and the already existing quality-oriented mindset of our employees all contributed to this.
One of the biggest benefits of having a matrix certification is that we need to work with only one certification body, which audits one system instead of the three that we previously had. Therefore, this adjustment obviously resulted in cutting expenses and saving time. In addition, as we now use standardized processes and tools, the cooperation between countries in this area is also easier and more efficient. And finally, as processes have been simplified through harmonization, we are able to respond faster and better to customer requests regarding quality and sustainability.
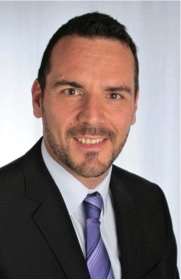
“The ISO matrix certification enables us to better support each other across these nine locations, through sharing experiences and best practices in quality management, occupational health & safety and environmental issues. I am proud of this achievement, which is the result of the successful cooperation of our QHSE (Quality, Health, Safety, and Environment) teams in Germany, Austria, and Switzerland. We are confident that this experience can serve as a blueprint for future projects at more sites.”
René Minder, Deputy Vice President Quality, Health & Safety, Environment, Operations AS EMEA