Occupational Health & Safety
9 minThroughout our business and most especially in our manufacturing sites worldwide, the health and safety of our employees is a priority.
Why it matters
The protection of the physical and mental integrity and well-being of employees is a core responsibility of dormakaba. Accidents and work-related illnesses can be of a long-term nature and entail costs to society and the company. We can only be successful in the long term if we help ensure our employees remain healthy. Occupational health and safety (OHS) addresses not only the safe operation of machines, ergonomic workplaces, and the handling of hazardous substances, but also mental health issues, including stress, depression, and emotional well-being. We strive simultaneously to create optimal working conditions for our employees and to ensure operational efficiencies.
Key activities
Throughout our business and particularly at our manufacturing sites worldwide, the health and safety of our employees is a priority. We want to provide a safe workplace, though injuries still occur in and around our facilities: including cuts, stumbles, commuting accidents, burns in smelting operations, heavy lifting, or exposure to toxic fumes in galvanization processes. Currently, dormakaba has only location-specific systems in place to align with national regulations and standards, as well as ISO 45001 certifications in larger manufacturing facilities.
Read about the outstanding occupational health & safety performance at our Nogales site
Read storyIt is our goal that, by the end of financial year 2021/22, all dormakaba manufacturing sites will maintain an occupational health and safety management system based on the rigorous standards set forth by ISO 45001. A total of 82% of our manufacturing sites have already achieved this. These sites have designated safety personnel, safety committees, regular safety training, and they collaborate with external partners to ensure that health and safety standards are integrated in prevailing production processes at dormakaba.
In addition, 24% of the manufacturing sites covered in this report benefit from ISO 45001 certification. Nine of our sites in Germany (Villingen-Schwenningen, Velbert, Bad Berka), Austria (Herzogenburg, Eggenburg) and Switzerland (Wetzikon, Rümlang, St. Gallen, Lausanne), for example, successfully implemented ISO 45001 standards in the financial year 2020/21.
To ensure our employees remain healthy, dormakaba focuses on three areas:
- Employee engagement and training
- Reducing hazardous materials
- Designated safety personnel and safety committees
Employee engagement and training
To identify and address our health and safety risks, employee engagement is crucial. Our employees are encouraged to report challenges and near misses in order to address these risks. Several segments, for example, regularly train employees to report near-miss incidents that have a potential for injury or property damage in an effort to be proactive. This program helps employees recognize hazards or unsafe acts and to correct them immediately or to ask for support to correct the issue. Near miss reports are treated the same as injury reports, and the respective supervisor follows up with the near-miss to ensure it is corrected.
Examples of our employee engagement and training activities in the financial year 2020/21 included:
- AS AMER at the Indianapolis (USA) facility installed safety blue lights on the vehicles and several dome mirrors at intersections, in order to reduce the risk of contact with pedestrians, as part of a comprehensive Forklift Safety Program. The facility stores hazardous waste in drums, which were equipped with automatic lids to ensure they are properly closed at all times. Thanks to its health & safety programs, the Nogales (Mexico) facility remained accident and injury free for almost 500 days. For its management of the Covid-19 measures and the implementation of essential business operating guidelines, the facility received external recognition from the government. Furthermore, AS AMER initiated conversations with employees on health & safety issues and implemented their suggestions for improvements. For example, in Chino (USA) they introduced daily discussions in an open forum style and in Montreal (Canada) they dedicated a whole month for health & safety awareness.
- AS DACH continued to implement operational health management systems in all departments in Germany, including defining roles and functions, and introducing measures designed to promote health and reduce sickness rates.
- AS EMEA offers regular health & safety trainings and supporting materials for employees. In UK & Ireland, each employee has their own health & safety training plan, and each field-based operative is also subject to unannounced audits to ensure they are working in line with their training. Regular Toolbox Talks discuss different health & safety matters, for example Covid-19, working at height, use of ladders, and hypodermic needles.
Reducing hazardous materials
The potential impact on employees’ health of working with hazardous materials is of special concern. Hazardous materials are used as cooling lubricants, as oils in machining and for the cutting of raw materials. They are also used in the electroplating process to protect materials from corrosion.
Examples of our activities to reduce hazardous materials in the financial year 2020/21 included:
- The AS DACH manufacturing facility in Suzhou (China) completed renovations to the painting system in order to switch over from solvent-based to water-based application.
- AS EMEA at the Herzogenburg (Austria) facility established a new nickel bath in the electroplating process, which allows longer operating time, reduces the amount of chemical waste, and improves occupational health & safety. COSHH (Control of Substances Hazardous to Health) Assessments and Material Safety Data Sheets are available for all substances used by our operatives in the UK & Ireland. The COSHH register is regularly reviewed and any hazardous substances that cannot be adequately controlled are removed accordingly. Air quality testing has been carried out on our Tiverton (UK) site and levels of dust, nickel, ethanol, and propane were found to be far below the local workplace exposure limits. In Wetzikon (Switzerland) we have set up a database monitoring the management of over 200 hazardous substances.
- Key & Wall Solutions at the Vittorio Veneto (Italy) plant installed 2 evaporators and reduced liquid hazardous waste coming from the nickeling and milling process by about 90%.
Designated safety personnel and safety committees
dormakaba employs designated safety personnel and safety committees in order to ensure that workers comply with company policies and government regulations. These forums also facilitate communication and cooperation between management and personnel.
Examples of our safety personnel and safety committee activities in the financial year 2020/21 include:
- AS APAC has designated safety personnel in Taiwan and Chennai (India). In the manufacturing facility in Taishan (China) we established safety committees and a new EHS manager was appointed. In addition, the facility in Yantai (China) conducted an external safety audit, which, combined with internal knowledge sharing, helped to improve safety practices at the site.
- AS DACH started the implementation of health & safety management systems at 3 locations (Bad Salzuflen, Bühl, and Zusmarshausen).
Our performance
Among all our reporting sites – including offices – 20% have a health and safety management system certified to ISO 45001 or the equivalent local standard; and 70% maintain a health and safety management system. For these sites, health and safety training goes beyond the mandatory requirements to include emergency and risk prevention. For example, assessments of repetitive movement and heavy load-lifting, to prevent work-related illnesses, take place at various sites.
85% of our employees are covered by a health & safety management system
Segment |
| ISO 45001 Certificate |
| Maintain OHS Management System |
AS AMER |
| 1 |
| 18 |
AS APAC |
| 2 |
| 15 |
AS DACH |
| 3 |
| 10 |
AS EMEA |
| 12 |
| 20 |
KWS |
| 2 |
| 8 |
Total |
| 22 |
| 65 |
% locations covered in reporting scope* |
| 20% |
| 70% |
% employees covered (versus Group-wide FTEs) |
| 23% |
| 85% |
*Including offices
In the financial year 2020/21, 186 occupational injury cases were registered, compared to 231 in the previous reporting year. This is a recordable injury rate of 1.4 compared to 1.7 in the previous reporting year1). There was an even split between injuries resulting in less than 3 days of lost working time and those resulting in more than 3 days of lost working time. Cuts were the most common type of accident, and most injuries were sustained to arms or hands. Most accidents occurred in production plants, with the second highest occuring during installation or service at customer sites. The most common root cause has been reported as lack of concentration. Through our global injury incident reporting tool, we have tracked over 200 corrective actions being implemented. The majority of corrective actions have been organizational safety measures. There were no fatalities as a result of work-related injuries in the financial year 2020/21, nor were there any high-consequence injuries reported.
- Recordable work-related injury rate = Number of recordable work-related injuries / Number of hours worked * 200,000
Outlook
We will continue our efforts to ensure our employees remain safe and healthy. Planned projects and initiatives include:
- AS AMER will focus on implementing or expanding EHS training programs and systems at the Indianapolis (USA) and Montreal (Canada) facilities to more effectively train employees and strengthen overall safety culture. The Nogales (Mexico) site plans to pursue ISO 45001 certification.
- AS DACH plans to certify the Bad Salzuflen, Bühl, and Zusmarshausen (Germany) sites to ISO 45001.
- AS EMEA will implement health & safety management systems based on ISO 45001 in Moscow (Russia), Budapest (Hungary), and Warsaw (Poland). In the UK & Ireland the reporting process on health & safety issues will be improved, and the HSQE team will increase field visits to service branches. In addition, the vetting process for sub-contractors is being reviewed and the approval criteria amended as necessary to ensure compliance is met with all sub-contractors.
Outstanding occupational health & safety performance in Mexico
Our manufacturing facility in Nogales (Mexico) received external recognition for health and safety management related to the Covid-19 pandemic. The facility also achieved almost 500 days with no accidents or injuries, as a result of effective leadership and employee cooperation.
The Covid-19 pandemic forced numerous companies to decrease production or even shutdown operations in case protective measures could not be applied. During these challenging times, the dormakaba facility in Nogales could continue working unaffected as an essential business, as a result of implementing and exceeding most of the preventative measures recommended by the Mexican health authorities and adjusting the internal guidelines and procedures.
For meeting the highest standard of the federal Covid-19 compliance program, the facility was granted the Mexican Social Security Institute’s Sanitary Security Protocol certification. The program included, among others things, employee trainings on health & safety, protective measures, workforce management, safe “return to work” guidance, and temporary pandemic policies.
The Nogales facility also received the Optimal Sanitary Performance certification from the prestigious International Society for Societal Performance & Kaufman Center for their outstanding achievement in keeping the pandemic under control in the plant. During a 3-month project a multifunctional team of our employees collaborated with experts from universities in Argentina, Spain, and Mexico to evaluate the effectiveness of the measures. As a result of this cooperation, they also created a best practice manual, customized for the Nogales facility and our employees.
The team in Nogales also deserves acknowledgment for another extraordinary achievement, namely being injury- and accident-free for almost 500 days. A long list of measures contributed to this accomplishment. This included the annual health, safety and environment training program (312 training hours in total), daily communication and awareness-raising at the beginning of each shift, the powered industrial vehicle and the machine guarding program, and job safety analysis, among other things. Furthermore, the plant is STPS (OSHA equivalent) certified for occupational health & safety.
“We are proud what we have achieved this year, but most of all, we are proud of the employees who helped us reach the goals we set for dormakaba Nogales. Thanks to their efforts, we managed to keep our employees safe during the pandemic.” - Q. Adalberto Vega Garcia, EHS Supervisor, AS AMER
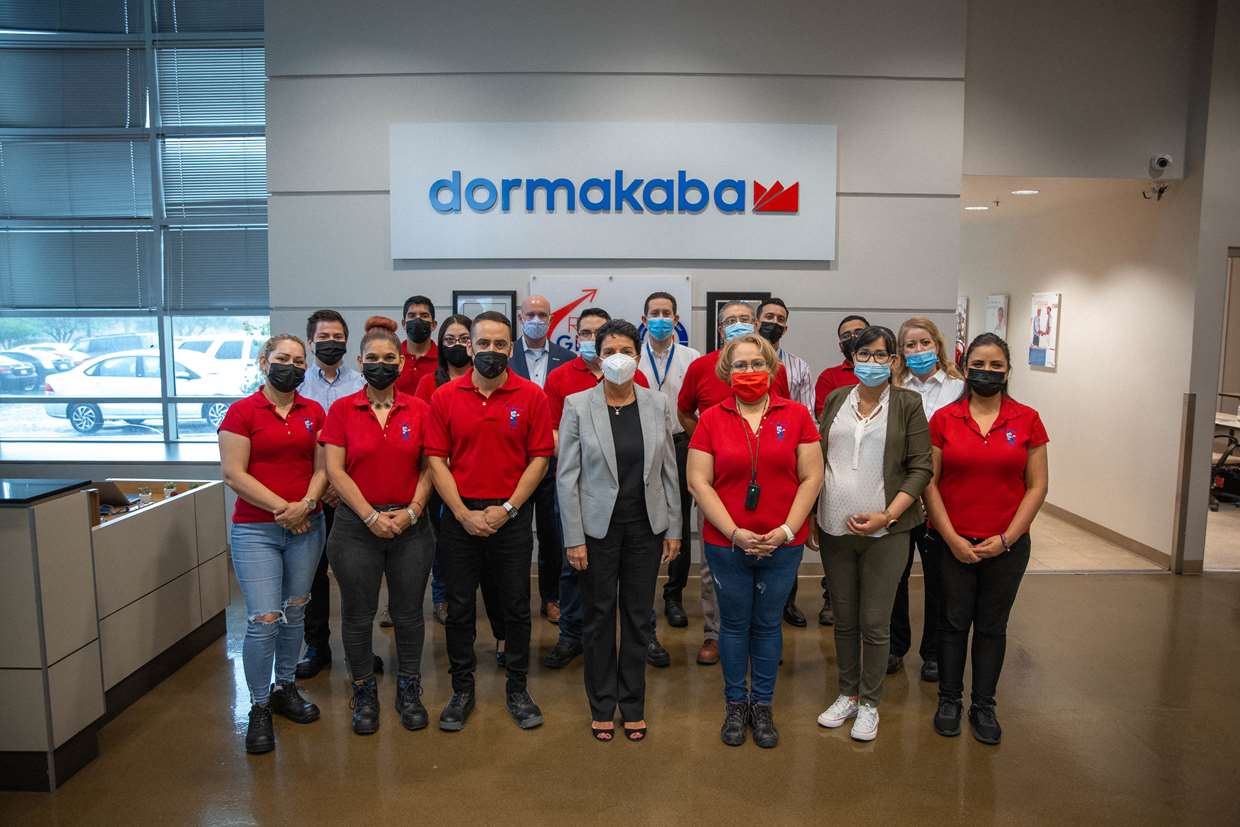