Customer Health & Safety
12 minTo fulfill the building requirements in the public and private domains, dormakaba products must meet very high standards of security, transparency and quality.
Focus Area: Products
To meet these prerequisites, dormakaba labels our products according to the applicable standards and customer requirements. Product management is responsible for this in close consultation with product development as stipulated in the Group Directive Adaptive Innovation Methodology (AIM) defined by Group Innovation Management. Internal and, if required, also external product quality assurance ensure that products have all the necessary labels. No product can be installed in field or released for production without the appropriate certification in hand. This is a necessary step in the product development life cycle, i.e. product verification phase, based on AIM.
Public buildings must meet high standards in terms of the health and safety of the people using these buildings. dormakaba meets these prerequisites with product certifications according to internationally recognized standards such as EN, ANSI or DIN. Particular attention is placed on the DIN 18040 standards, which applies to barrier-free construction in public buildings.
dormakaba brings added-value to our customers by implementing features which make doors easier to open, benefiting the elderly or mobility impaired, as in the case of the TS 93 and TS 98 door closers.
Wherever applicable, products developed in the AS AMER segment are scrutinized for compliance to two major regulatory requirements which includes a third-party certification for safety performed at the Underwriter’s Laboratory (UL), Intertek, or self-certified laboratory and third-party certification for compliance to electromagnetic interference and compatibility as per the Federal Communications Commission (FCC) standards in the USA.
dormakaba ensures compliance to 12 various UL standards, which includes fire testing and standards on marking and labeling systems. An example of the UL test (UL 10C: Fire tests of door assemblies) requires the door assembly with the locks to be placed in a frame and subjected to a temperature of 1052⁰C for a period of 3 hours. Requirements are met if no flaming occurs on the unexposed surface of a door assembly during the first 30 minutes of the testing period, among other prerequisites. Fire testing according to DIN standards is also conducted.
Furthermore, products are designed to comply with the RoHS (Restriction of Hazardous Substances Directive 2002/95/EC). All components and materials are determined to be RoHS compliant before implementation in products during product development.
dormakaba also designs to ensure compliance to applicable Builders Hardware Manufacturers Association (BHMA) codes depending on the product line. The BHMA is the trade association for North American manufacturers of commercial builders hardware. BHMA is involved in standards, code and life safety regulations and other activities that specifically impact builders hardware. Depending on the product line, whenever applicable, products are designed to meet the Florida Building Code (FL13061).
dormakaba also participates and at times, leads the creation, updates or revisions of existing BHMA standards. BHMA standards are voluntary and thus enables dormakaba to demonstrate leadership towards product quality and safety.
Customer health and safety is addressed similarly within segment AS APAC. Further, the topic is integrated in the ISO 9001 management systems at various locations. The focus for AS EMEA, which develops various Electronic Access and Data (EAD) products, is also on product certification. For example, the Kaba Wireless Gateway 90 42 is certified to EN 55024, which tests for immunity in cases of electrostatic discharges, power surges and interruptions, or radio frequency interference. The product is also certified to IEC 60950, which specifies requirements intended to reduce risks of fire, electric shock or injury for the service person, operator or end user who may come in contact with the product.
In Segment AS DACH, automatic doors are subject to the highest safety demands in accordance with EN 16005. To meet these, self-monitoring sensors are mandatory. Obstacle self-detection and automatic reversing are also included in many products. For example, Talos CSD circular sliding doors and the Talos RDR revolving doors feature a safety sensor system. Emergency exit and escape route doors are equipped with a redundant operator, an additional control unit for safety purposes and a self-monitoring motion detector. The ES 200-2D door operator features emergency opening following a power failure. The FFT FLEX Green is certified to user safety and performance standards based on EN 16361. And revolving doors such as the KTV3 and KTV 4 require a safety risk assessment before installation in accordance with DIN 18650. This is provided by dormakaba at the building site before a sale is made.
Supporting ease of access
The TS 98 XEA door closer features our EASY OPEN technology, which provides barrier-free access based on German Industrial Standards DIN SPEC 1104 and DIN 18040. The heart-shaped cam technology reduces the required effort to a minimum, with 40% less effort. It not only opens easily, but also features delayed closing. This allows sufficient time to pass through the door with luggage, prams, hospital beds and similar.
TS 98 XEA with EASY OPEN: heart-shaped cam
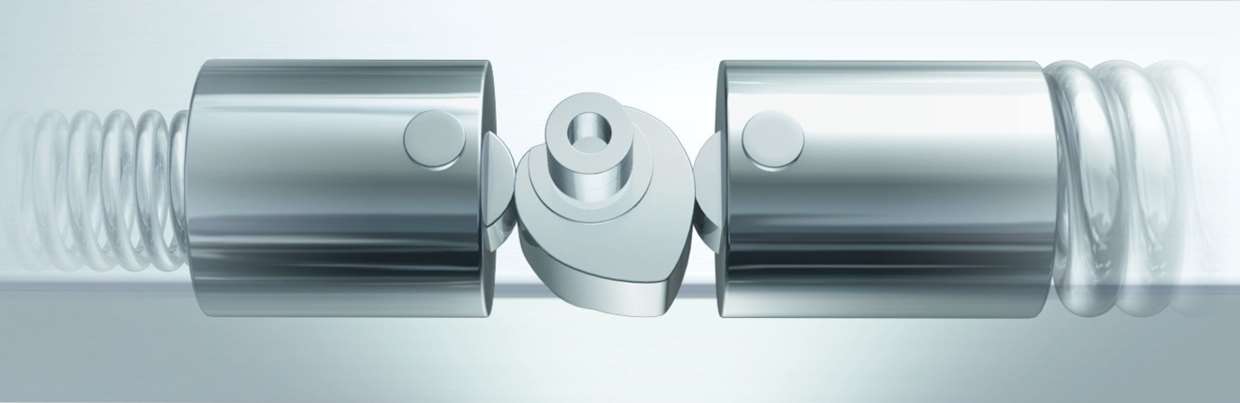
Grievance mechanism
dormakaba has a Group-wide customer complaint process in place based on the principles of ease of access, solution-driven expertise, short response times, positivity and focus on the company value Customer First.
The process follows five steps:
- Acknowledge that the customer has an issue, ideally within 24 hours
- Assess the problem, prioritize and find a solution driver
- Resolve the issue
- Respond in a timely manner, keeping the customer informed on the status
- Conclude with a proper follow-up to assess the customers satisfaction and integrate lessons learned
Regulatory compliance falls at the top of the list of priorities for any development leads and require immediate action plans. An incident response plan is put in place to enable direct access to the required resources as well.
Evaluation of the management approach
The management approach is evaluated based in benchmarking of competitor’s product positioning, through internal or external verification in terms of certifications (including ISO 9001) and testing, and through stakeholder feedback.
For the latter, dormakaba analyzes inputs from customers and end-users prior to product launches. In segment AS AMER, all new product launches require the product development team to initiate an alpha (internal) and, in most cases, a beta (external) testing. Beta testing is the process by which the first initial products released from the production lines are installed in a limited customer setting, monitored closely by the sales, product management and engineering team. During the beta testing, any issues can be escalated to the team, to which an investigation is carried out and issues resolved prior to the full launch of the product in the field. This provides an extra layer of verification and validation to most of the product launches and further deployments.
The management team regularly communicates any product shortcomings to ensure that we have an enhanced level of attention to these and ensure that we learned from any potential gaps. Segment AS AMER has dedicated manpower to ensuring that any corrective actions requiring an update in processes are implemented accordingly. This ensures that there is neutral individual who can implement new processes segment-wide that will be common and applicable to everyone.
Further, segment AS APAC conducts customer satisfaction surveys on an annual basis and the segment management conference includes Voice of the Customer sessions to gather additional insights to product performance, health and safety topics. In the spirit of continuous improvement, resources are allocated to ensure that there is no compromise with regards to product safety and regulatory standards. The segment goes beyond by allocating resources to joining committees to help improve and shape future standards and industry requirements. The segment is thus actively helping raise the bar regarding various criteria.
Business Unit Key Systems approaches the topic of Customer Health & Safety as an element of its ISO 9001 certifications and ensures compliance with both mandatory (such as the European CE declaration of conformity) and voluntary safety standards. Over 16 product certifications apply. Business Unit Movable Walls has over 10 active certifications, including from Underwriter’s Laboratory (UL) and the Canadian Standards Association (CSA). Product certification includes fire testing, smoke testing, ball-throwing tests, and weight bearing tests on suspension track systems, for example. The related legal registers are regularly surveilled and updated.
Each Key Systems product features proper documentation such as owner’s manual, declaration of compliance, contact details to the manufacturer, quick guides, tutorials available on the web and even trainings on demand or during product installation to provide the customer with all the information relevant to correct product use and safety features. Regional distributors are periodically trained on the same topics.
Grievance mechanism
Besides the Group-wide dormakaba customer complaint process as described in the Access Solutions Segments section above, the ISO 9001 quality system within Key Systems includes a further grievance mechanism. Each production site implements their ISO 9001 processes locally. Quality assurance managers have the ownership of the grievance mechanism and track any complaint from receipt to its closure, including feedback to the customer. This includes registration of the complaint in the ticketing system, evaluation, problem analysis and corrective actions, verification, lessons learned, and closure. The intended users are all the relevant stakeholders such as customers, technical assistance, procurement, quality control, logistics, manufacturing, product development, and sales teams. Effectiveness of the grievance mechanism is based on number of open, accepted, refused and closed complaints per fiscal year.
Evaluation of the management approach
The management approach is evaluated firstly through external audits by ISO 9001 certification bodies. Product surveillance (e.g., UL, CSA) and customer audits also take place. Further, the customer claims monitoring and database mentioned as part of the grievance mechanism is also considered in defining corrective actions. At least once a year, a management review assessment evaluates related KPIs and performance status. Movable Walls subsidiary Skyfold (Canada) also engages with customers through surveys.