Occupational Health & Safety
9 minThroughout our business and most especially at our manufacturing sites worldwide, we respect the human right to safe workplaces.
Our approach
All workers share the human right to safe and healthy working conditions, and as an employer we do our utmost to protect the physical and mental integrity and well-being of our employees. Accidents and work-related illnesses can be of a long-term nature and entail costs to society and the company. We can only be successful in the long term if we help ensure our employees remain healthy. Occupational Health & Safety (OHS) addresses not only the safe operation of machines, ergonomic workplaces, and the handling of hazardous substances, but also mental health issues including stress, depression, and emotional well-being. We strive to simultaneously create optimal working conditions for our employees and to ensure operational efficiency.
Our activities
We have already put in a lot of effort to provide a safe workplace. Injuries can still occur in and around our facilities, including cuts, stumbles, commuting accidents, burns in smelting operations, injuries due to heavy lifting, or exposure to toxic fumes in galvanization processes. Currently, we have location-specific systems in place to align with national regulations and standards, as well as ISO 45001 certifications at larger manufacturing facilities. Our goal is that by the year 2027 we will decrease the recordable work-related injury rate by 33% (baseline 1.4 in FY 2020/21).
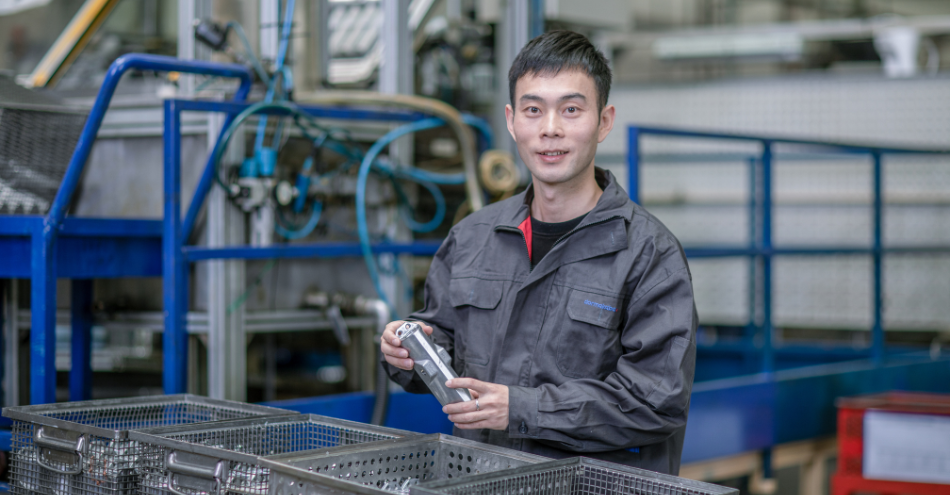
Risk analysis and preventative actions
We have been using root cause analysis of injury incidents globally to identify and implement the corrective actions necessary to prevent repeat incidents. A further example of preventative processes is the Corrective Action Read Across Program in the Americas, initiated in FY 2021/22 with the goal of reducing potential injuries by implementing corrective actions regionally. All investigations into recordable injuries are assessed to determine whether the corrective actions may be applicable at other locations. The key idea behind the program is that every injury is an opportunity to prevent the same thing from happening in the future at other locations.
“A critical component in any injury investigation is the implementation of effective corrective action. Many of our locations have similar processes, equipment, and conditions where the same injuries could also happen. The Corrective Action Read Across program has strengthened our safety culture in the Americas. Within the first year of implementation, we have already deployed over 35 corrective actions throughout our facilities.” - Kristin Jarrett, AVP EHS Region Americas.
To ensure our employees remain healthy, dormakaba focuses on three areas:
- Employee engagement and training
- Reducing hazardous materials
- Designated safety personnel and safety committees
Employee engagement and training
To identify and address our health and safety risks, employee engagement is crucial. Our employees are encouraged to report challenges and near misses in order to address these risks. Several regions, for example, regularly train employees to report near-miss incidents that have a potential for injury or property damage in an effort to be proactive. This program helps employees recognize hazards or unsafe acts and to correct them immediately or to ask for support to correct the issue. Near-miss reports are given the same emphasis and attention as injury reports, and the respective supervisor follows up with the near-miss to ensure it is corrected.
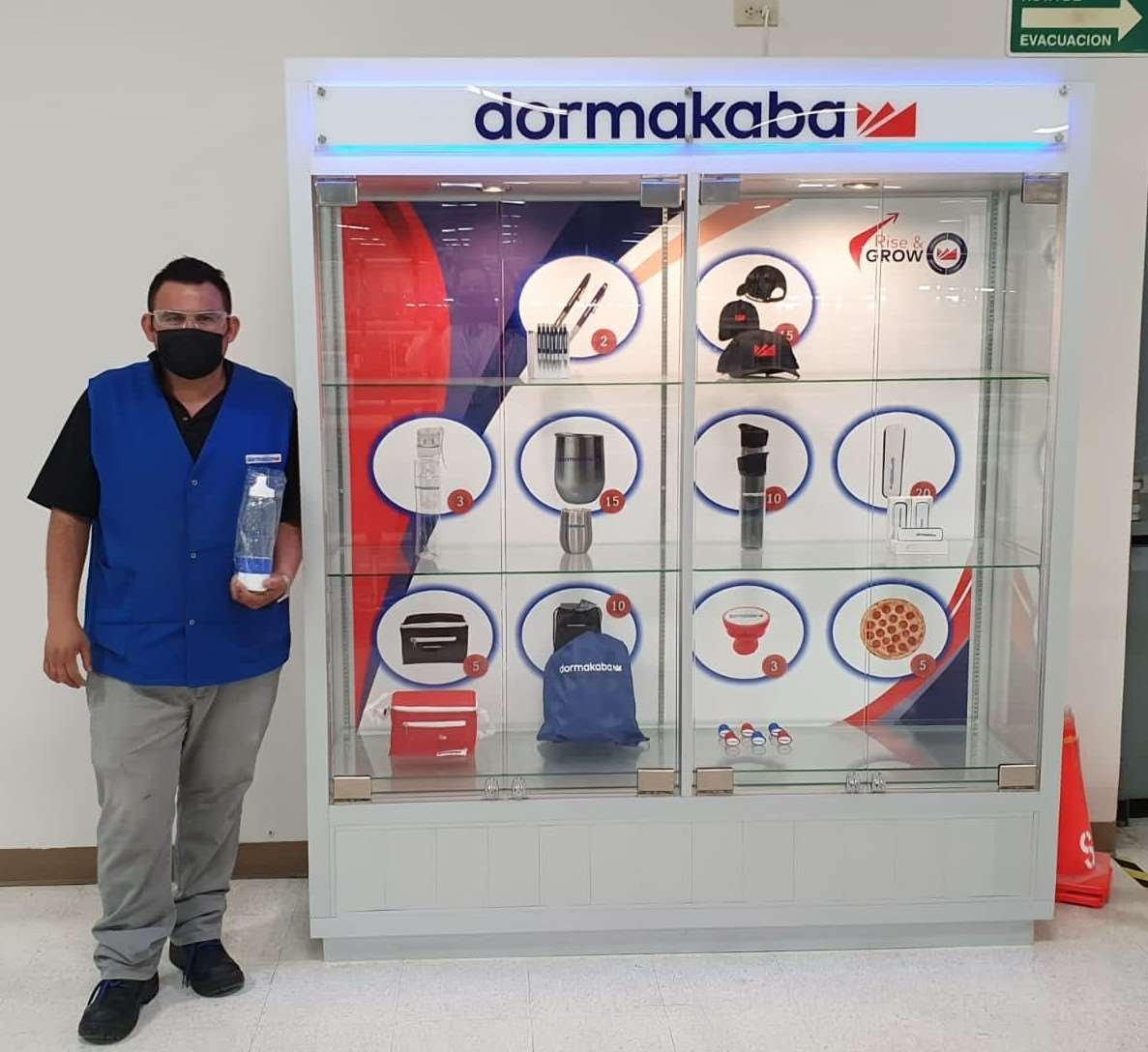
Proactively reporting safety suggestions
Across many sites, we have employee engagement programs in place that motivate employees to identify and report any near-miss incidents, unsafe acts and conditions. For example, in Melaka (Malaysia) we have Hazard Identification Tags, in Singapore we have the STOP for Safety Program and in Nogales (Mexico) the Improvement Ideas Program to motivate employees to submit their safety suggestions and their ideas are rewarded.
The similar Me Safe Program in Dyersville (USA) also collects employee ideas, which are evaluated by the local EHS Coordinator. Once approved, actions are implemented, and the employee gets immediate recognition. Between July 2021 and April 2022, 320 suggestions were submitted in Dyersville, resulting in a drop in the Total Case Incident Rate from 8.8 to 4.7.
“We want everyone to be involved in the safety process by helping identify hazards and making recommendations to improve safety. The employees in the manufacturing area understand the process best and often have the greatest ideas. The Me Safe Program gives employees a voice that is heard and also helps to improve the communication between management and manufacturing. Safety is one thing we all have in common and an interest in seeing it succeed." – Kerry Bartlett, EHS Engineer at Modernfold in Dyersville.
During FY 2021/22, we launched several health and safety trainings locally. These included a CPR training in Singapore with 56 participants, a general health and safety training at all locations in Sweden for about 100 participants, safe driving courses and emergency trainings on fire control, evacuation, and first aid in Spain and Portugal, as well as training on potential health and safety risks and the implementations of 5S practices in San Jose (USA).
Reducing hazardous materials
The potential impact on employees’ health when working with hazardous materials is of special concern, and we seek to eliminate or reduce their use as much as possible. Hazardous materials are used as cooling lubricants, oils in machining, and for the cutting of raw materials. Some hazardous materials are used to protect materials from corrosion in the electroplating area as well.
Key activities during FY 2021/22 included:
- In Melaka (Malaysia), HMT-11 has been replaced by the less harmful LK-11 during the metal treatment process. Furthermore a dust collector system has been implemented. As a result of the replacement, chemical exposure monitoring showed 0.046 mg/m3, which is considerably less than the permitted exposure limit (10.0 mg/m3).
- In Suzhou (China), a solvent-based tetrachloroethene (PERC) component washing machine has been replaced by a water-based one, avoiding 20 tons of PERC annually. Another key project at the site was the renovation of the closers washing machine (Y-degreasing), which included the installation of a new distillation machine and a chiller device. The main function of distillation is to remove oil from PERC and to ensure a good cleaning quality. The oil removed from the distillation machine is disposed for special treatment by a qualified third party. As a result of this upgrade, we were able to reduce PERC consumption by an additional 20 tons (from 35 to 15 tons).
- In Rocky Mount (USA), the hydrochloric acid was replaced by pre-mixed boric acid salt, which reduced the chemical handling hazard, improved the quality of the product plating, and even reduced product scrap.
Designated safety personnel and safety committees
dormakaba employs designated safety personnel and safety committees in order to ensure that workers comply with company policies and government regulations. These forums also facilitate communication and cooperation between management and personnel. The key responsibilities of the committees are to define and review safety strategies, policies and metrics, discuss incidents, and disseminate safety information.
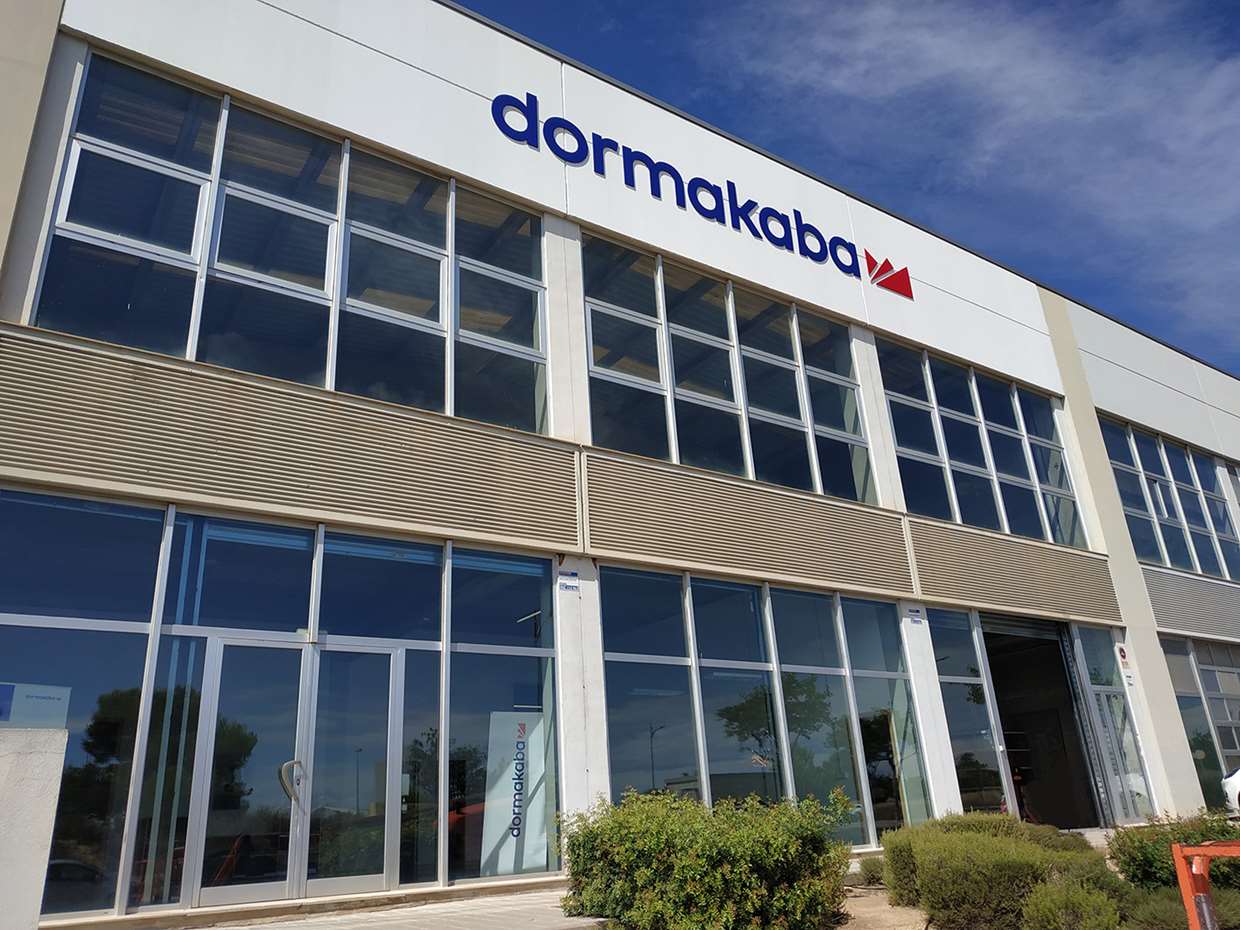
Outstanding Health & Safety results in dormakaba España
Good action plans and processes, clear communication, employee engagement, and the support and commitment of the management team are key to achieving positive health and safety outcomes. A dedicated team in Spain and Portugal strive to create optimal working conditions for their approximately 160 employees. Below are some of their key activities and achievements:
- Accidents and injuries must be reported in the dedicated system and analyzed on the same day. Both local management and employees are informed of the issue and the possible corrective actions to prevent similar situations in the future.
- They regularly launch health and safety trainings, for example on safe driving habits and emergency topics, like fire control and evacuation.
- At the beginning of each meeting at the Iberian sites there is a “safety first” discussion, including KPIs and their status. Moreover, employees can access a dedicated online platform for health and safety information, and they can also collaborate by sharing improvement ideas through an email account.
- Before moving to a new location in Valencia, the team ran ergonomic evaluation studies both on physical load and the adequacy of machines. The workstations in the new facility were defined according to the results of the study. A conveyor belt was designed especially for this location to increase productivity and reduce discomfort at the same time.
- In March, dormakaba España was certified with the ISO 45001 standard, and the site already had a plan in place to go beyond the requirements of the certification, through detailed internal audits and risk assessment updates.
- dormakaba España goes beyond its responsibility for its own employees and has started a collaboration with key installation partners to improve their health and safety systems, thereby contributing to customer health and safety too.
Our performance
87% of our employees are covered by a health & safety management system
ESG Performance TableAmong all our reporting sites – including offices – 28% have a health and safety management system certified according to ISO 45001, and 71% maintain a health and safety management system. For these sites, health and safety training goes beyond the mandatory requirements to include emergency and risk prevention. For example, assessments of repetitive movement and heavy load-lifting, to prevent work-related illnesses, take place at various sites.
In FY 2021/22, 198 occupational injury cases were registered, compared to 186 in the previous reporting year. This is a recordable injury rate of 1.5 compared to 1.4 in the previous reporting year1). Of these, 92 cases were expected to result in more than three days of lost working time. Cuts and bruises were the most common types of injuries, and most injuries were sustained to the arms and hands. Most accidents occurred in production plants, with the second highest occurring during installation or service at customer sites. The most common root cause has been reported as lack of concentration. Through our global injury incident reporting tool, we have tracked over 268 corrective actions being launched in FY 2021/22. The majority of corrective actions have been organizational safety measures. There were no fatalities as a result of work-related injuries, nor were there any high-consequence injuries reported.
- Recordable work-related injury rate = number of recordable work-related injuries / number of hours worked x 200,000
Outlook
Our focus in FY 2022/23 will be the reduction of injury rates across 45 locations by 5.5% versus the previous year. This includes initiatives such as behavior-based safety awareness training, the formalization of monthly safety audits, and Hazard Walk-throughs at the manufacturing plants. Some locations will focus on improving protective personal equipment or changing work processes to reduce manual handling, including implementing semi-automated polishing processes.