Circular Economy & Materials
18 minWe are accelerating circular solutions to develop material-efficient, energy-efficient, high-quality products that reduce our customers’ environmental impact and meet the needs of a sustainable built environment.
Our approach
We live in and depend on an interconnected world, with complex environmental, social, economic, and cultural systems. Damaging one element may cause unexpected impact elsewhere. We understand the limits of our planet and that we must act more sustainably in order to meet increasing social and economic demands. As a leading manufacturer, dormakaba is committed to incorporating the latest product life cycle approaches and environmental technologies to continuously advance our product development and improve our own as well as our customers’ sustainability performance. This not only provides new opportunities for our design and manufacturing processes; it also addresses our customers’ expectations regarding environmentally friendly products.
Our Group-wide Environment Directive regulates minimum business standards in manufacturing practices, product circularity, and eco-design, including material selection and the energy efficiency of the product use phase. The dormakaba sustainability commitment and life cycle approach are also integrated into the company’s Product Design Manual.
A circular economy provides solutions for some of the key global challenges by eliminating waste and pollution and circulating products and materials.
Our Circularity Approach

Our activities
Learn about our activities and key results regarding value chain emissions (Scope 3) from purchased goods & services, and the use of sold products.
Energy & EmissionsProduct design with the circular approach
With an average life span of 40 to 50 years, buildings should ideally be constructed in a way that allows the required materials and natural resources to be used efficiently. We are dedicated to producing high-quality and reliable products and solutions, while also integrating our customers’ desire for environmentally friendly options. As a result, product design remains a core focus of our sustainability strategy, with an emphasis on energy consumption and carbon emissions during the product’s use phase, waste management, and recyclability at its end of life.
Our sustainability commitment and sustainable design criteria are integrated into our Product Design Manual, which is binding for all new dormakaba-branded products. By 2023, we plan to cover all new product developments and optimizations with our circularity approach.
Life Cycle Assessments (LCA) provide a reliable calculation of the environmental performance of a product. This includes the systematic assessment of the environmental impacts arising during the extraction of raw materials, through production, distribution, and use phases, which are quantified based on materials, energy consumption, transport routes, emissions, and the life span of the products.
There are two LCA approaches: cradle-to-gate and cradle-to-grave. The first approach considers all production stage modules: raw material supply, transport, and manufacturing. The latter covers all life cycle modules, which means that in addition to the cradle-to-gate stages, cradle-to-grave analyzes the building construction process, the product use stage, and end of life (i.e., the upstream value chain). We mainly use cradle-to-gate “with options” so that we can select the relevant upstream life cycle module(s).
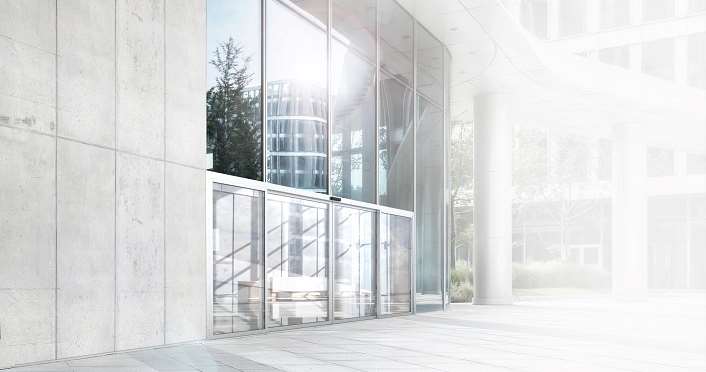
Digital energy calculator for the product use phase
In terms of primary energy consumption, the building sector is one of the largest energy users in the world – as a result, its influence on climate change is enormous. Therefore, we have set a target of having best in class energy efficiency for new products by 2023. In FY 2021/22, we launched the ST PRO Green RC3 in the Austrian and Swiss markets, for example, which is a new, energy-saving automatic sliding door with a thermally separated profile system that reduces energy loss in the building due to a very low heat transfer coefficient.
Our digital Product CO2 Inventory Tool provides information on the carbon emissions of energy-consuming products during their use phase. This supports product development and optimization activities to create more energy-efficient products and also contributes to our target of decreasing Scope 3 emissions from the use phase of sold products.
The Product CO2 Inventory Tool includes the footprint of around 350 products that consume energy after installation, including those that are battery-operated or connected to the electricity grid. Through the tool, our Product Managers and Engineers are able to continuously check and improve data quality based on product parameters, easily make updates to include new products, and have a better understanding of where the biggest impact is taking place.
The tool collects information for example about the products’ lifetime, the number of operating days per year, energy consumption and related features. The parameters are in line with requirements found in the Environment Directive (see section B.9). Based on the number of sold products and country-specific emission factors, we are able to determine the greenhouse gas emissions for the whole lifetime of a product. Our calculation method is in line with the GHG Protocol.
Designing environmentally friendly packaging
For the packaging of our products, we mostly use plastic, wood, paper, and cardboard. It is our aim to substitute packaging materials with more sustainable alternatives. By 2027 we want to use zero fossil-fuel based plastic in our packaging (baseline 223 tons in FY 2020/21) and 100% of paper, wood, and carton used should stem from Forest Stewardship Council (FSC)-certified sources. We have started exploring possibilities, and at our Vittorio Veneto (Italy) manufacturing site, it is already the standard to use FSC-certified packaging.
Providing transparent information about our products
As of early 2021, components imported or sold in the European Union, with Substances of Very High Concern (SVHCs) in a concentration higher than 0.1% must be reported in the so-called SCIP Database, created by the European Chemical Agency. To be compliant with European regulations, we are continually uploading the required data on SVHCs to the SCIP database. Furthermore, we adhere to the requirements of the RoHS Directive 2011/65/EU, which restricts the use of certain hazardous substances in electrical and electronic equipment.
Product declarations and green building certifications
We quantify and disclose a product’s environmental impact through its entire life cycle in our Environmental Product Declarations (EPDs), which are based on the international standards ISO 14025, 14040, 14044 and the European standard EN 15804. Our EPDs meet all mentioned standards to ensure that our environmental information is transparent, reliable, and credible.
dormakaba also offers various health-related product declarations which transparently account for the materials found in our products. These take the form of Health Product Declarations (HPDs) or Building Product Declarations (BPDs), depending on local market requirements.
By 2027, we aim to double our sustainability-related product declarations/certifications, including Cradle to Cradle and for recycled content (baseline 170 in FY 2020/21). To date, we can provide our customers with 200 such declarations and certifications. By providing transparency regarding our sustainability performance, we secure our market position and offer added value to customers seeking green building certifications.
Product information from environmental or health-related product declarations can contribute to Building Information Modelling (BIM) and specifications or help attain the highest levels of green building certifications, such as Leadership in Energy and Environmental Design (LEED). dormakaba publishes the product information on internationally recognized sustainability platforms such as the Sustainable Product Information Module (SuPIM) by the Institut Bauen und Umwelt (IBU). SuPIM provides all product-related sustainability data from the manufacturers for various building certification systems such as DGNB, BNB, LEED, and BREEAM. These are compiled in a data sheet and supplemented by the corresponding verification documents. For quality assurance purposes regarding the underlying documents, IBU offers manufacturers a review of the entered data.
Such databases provide transparent environmental and health information for users and ensure easy access to specific product data. By providing this level of product information, we seek to lower market entry barriers in the green building industry, enabling our inclusion in related bidding processes.
Production with lower environmental impact
Activities and key results regarding carbon emissions (Scope 1 & 2) and energy consumption during production.
Energy & EmissionsAt dormakaba, we recognize that environmental responsibility is integral to producing world-class products. Besides adhering to environmental laws and regulations, we focus on improving our management of environmentally relevant processes and on monitoring and reducing our energy consumption, carbon emissions, water consumption, and effluents, as well as monitoring our waste disposal and recycling rates.
Responsible use of materials
Historical information on material use.
ESG Performance TableAmong the raw materials we use for our products, there are metals such as steel, brass, aluminum, nickel silver, and zinc, as well as gypsum board, glass, and plastics. Since the primary extraction of metals from ore and the subsequent refining processes are resource-intensive, one key focus is to increase the use of metals with high recycled content. Other important materials are wood, paper, and cardboard, which are made from renewable resources.
Material use (in %)
Raw material use (in %)
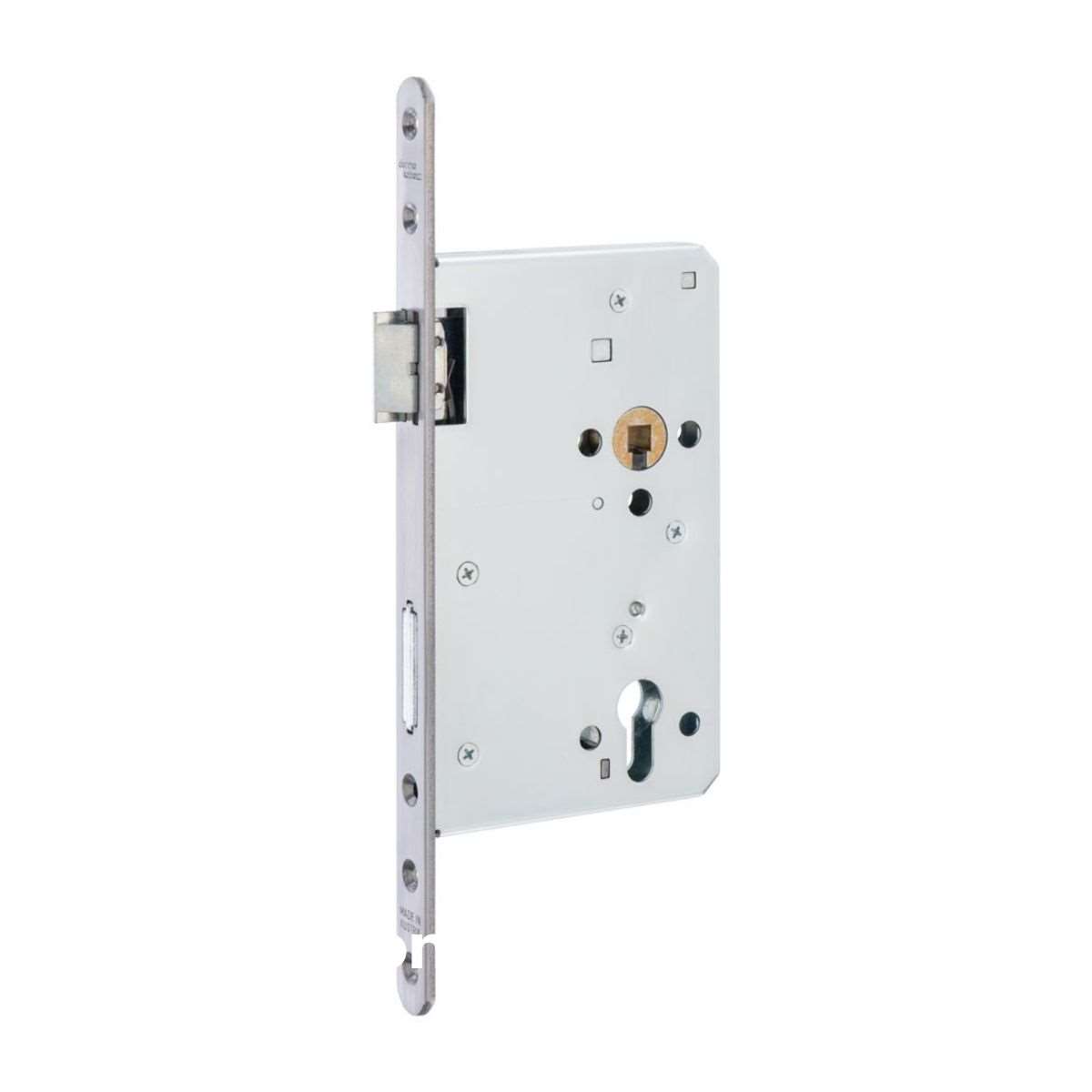
Successful substitution of materials with lead content
The heavy metal lead (Pb) is often used as a minor addition to alloys found in components of our products, to improve their mechanical properties. This allows better and more efficient machining and cutting, and thus plays a key role in our production processes and in the quality of our finished products. It is challenging to substitute it, and we are continuously searching for solutions by taking part in industry-wide discussions and through own R&D.
In the previous year, Key & Wall Solutions redesigned several steel components with high lead content and started the sale of lead-free steel keys in the Region Europe & Africa. During FY 2021/22, we were able to substitute brass with eco-brass in one component of our Lock Series 122, after thorough examination of this material’s specifications, including strength, elasticity, color, weight, and external testing. We are planning to substitute other small parts in several other products within our portfolio, as we have done for the c-lever coupling system.
Several production sites focus on closed-loop systems in their material use. The manufacturing facilities recycle most internal scrap metal, either back into their own processes or by selling it to a local approved recycler. Scrap material is also sent back to the original producer, who then uses it to make our purchased materials, resulting in a closed-loop system. Examples include:
- For over six years, the production facility in Vittorio Veneto (Italy) has had over 70% of produced scrap going back into its closed-loop system.
- The facility in Taishan (China) reuses zinc alloy scrap in the die casting process, while in Melaka (Malaysia), aluminum chips are remelted in the foundry for reprocessing.
- In Suzhou (China), the wooden pallets in which door closers arrive from Melaka (Malaysia) are reused for delivering other products to Singapore (approximately 610 pieces per year), where they are used for internal processes or provided to local suppliers, who use them to deliver other components back to the Suzhou plant. The Singapore team is investigating how to eventually circulate the pallets back to the Melaka plant.
Waste management
In addition to water consumption and effluents, waste management is of key importance during the electroplating, surface finishing, and painting processes. Our filter systems ensure that potentially hazardous substances are not released externally. Toxic waste arising from painting and electroplating is disposed of as special waste. Certified disposal companies are commissioned to dispose of industrial waste and chemicals, and to recycle materials.
We respect the universal human right to safe and clean drinking water and sanitation. Learn about our activities and key results regarding water and effluents management.
Human RightsThe generation of different waste streams is an inevitable consequence of our operations, although by implementing the circular economy approach, we aim to send zero waste to landfill in our operations by 2027 (baseline 3,443 tons in FY 2020/21). We monitor our waste by treatment method and waste type. At 74.6% by weight, the largest proportion of waste is scrap metal. In FY 2021/22, approximately 73% of the waste stream was recycled, reused, or recovered (including raw materials and energy recovery). In Dyersville (USA), for example, the wood sent to landfill has been decreased by 40%, as a result of the replacement of wooden crates with returnable containers, in which they receive glass from a supplier. In Le Mesnil St-Denis (France), waste is separated into nine categories. Today, approximately 95% of the waste generated on site is sorted according to these categories. Recycling is processed by specialized and certified companies, one of which employs people with disabilities or who are socially disadvantaged.
Non-hazardous waste by type
(in metric tons)
Hazardous waste by type
(in metric tons)
Waste by treatment path*
(in metric tons)
*On-site storage includes waste that is temporarily stored at the premises before being directed to treatment/disposal
Waste intensity
(t/mCHF net sales)
Take-back programs
All of our products have a long life span of up to 20 years, but their purpose should not end after deinstallation. Some of the components of our products can be reused, repaired, or reintroduced as raw materials back into the manufacturing cycle.
Collecting products and components from customers and partners requires collaboration between various dormakaba departments. Logistics, quality management, product development and production are all important functions that should be involved. Take-back programs have multiple benefits, such as stronger customer relationships, alternative supply of critical raw minerals, mitigated risks associated with hazardous materials handling, reduced environmental impact, and cost savings.
By 2027, we plan to offer extended producer responsibility take-back schemes for all products and packaging in ten top sales countries. During FY 2021/22, we started the development of a pilot program in Switzerland and Austria for locks and cylinders.
Outlook
During the next financial year, we will focus on the following activities:
- We have identified further products for which we will develop sustainability-related declarations/certifications, including pre- and post-consumer recycled content certifications. Additionally, we will develop circularity guidelines for new product developments.
- Together with an external consultancy, we will develop further benchmarks for high recycled content and energy efficiency.
- Our leadership teams in nine out of the ten top selling countries will develop detailed four-year action plans for launching take-back programs and to evaluate local recycling companies for partnerships.
- Lastly, 33 manufacturing sites will develop detailed zero waste to landfill action plans, showing how they will achieve a 25% reduction per year starting in FY 2023/24.