Customer Health & Safety
11 minOur vision is to make access in our customers’ lives safe, secure, and sustainable. End user health and safety is therefore a top priority and an inherent part of our business plans.
Our approach
As one of the top three global access control and security solutions companies, customer health and safety is fundamental to our sense of product responsibility. By identifying and minimizing all possible risks relating to our products – including those arising from harmful materials or potentially endangering functional features – we ensure the safety of our customers and end users.
Our activities
Public buildings must meet high standards in terms of public health & safety – this also applies to our built-in products and solutions. dormakaba meets these product and customer requirements with product certifications for internationally recognized standards such as the European Standard (EN), American National Standards Institute (ANSI), or the Deutsches Institut für Normung (DIN). We pay particular attention to the DIN 18040 standards, which apply to barrier-free construction in public buildings. Furthermore, ISO 9001 processes ensure that quality management requirements are continuously monitored and improved. No product can be installed in the field or released for production without the appropriate certification.
To ensure product- and solution-specific customer health and safety, our Access Solutions and Key & Wall Solutions businesses are developing adequate action plans.
Access Solutions
Our Access Solutions (AS) business provides products such as escape routes, entrance systems, and hotel access systems. We work to address fire safety, electromagnetic interference, and to reduce hazardous substances, as well as ensuring that emergency exits open following a power failure.
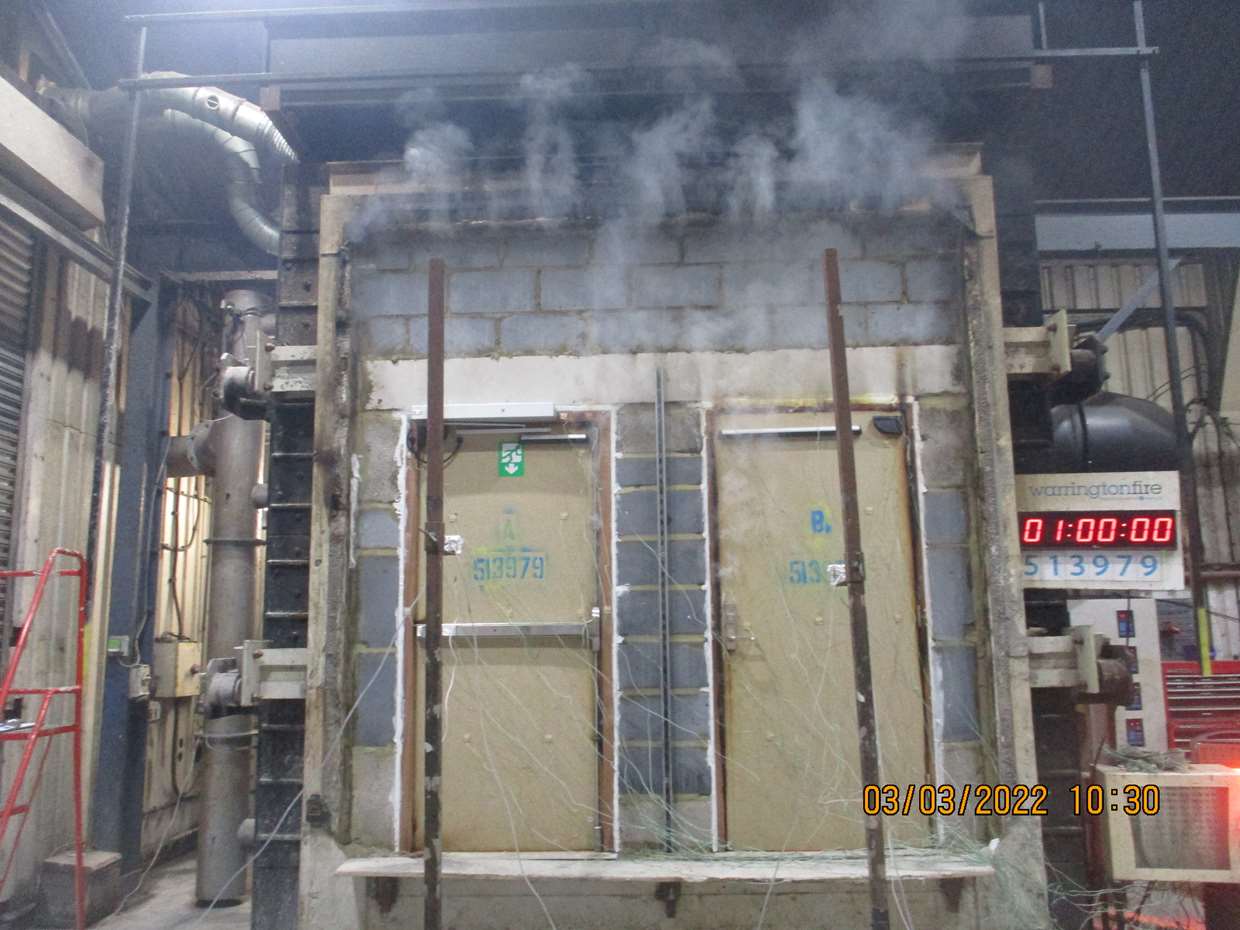
Fire testing of the ED 250 door operator
An example of a fire test requires the door assembly with locks to be placed in a door leaf and subjected to a temperature determined in the door leaf specification for a period of three hours. Requirements are met if no flaming occurs on the unexposed surface of a door assembly during the first 30 minutes of the testing period, among other prerequisites. The fire test fails if flames penetrate the door leaf at any point during the whole test time.
The dormakaba ED 250 door operator with flat scan and IRS door sensors underwent a successful fire resistance test (EI60) for continued Certifire Certification in FY 2021/22. After the product was installed in the fire door, it was exposed to fire for 73 minutes without flames spreading to the non-exposed side of the wall. The fire test results define the requirements for dormakaba engineers when it comes to the installation aspect of the sensors and their wiring.
Hazardous substances: products are designed to comply with the EU Directive on the restriction of the use of certain hazardous substances in electrical and electronic equipment (RoHS Directive 2011/65/EU and its enforced amendments, especially 2015/863/EU). All components and materials in electronic products sold in the EU market must be RoHS-compliant before any product manufacturing begins.

Outstanding VOCs test result for Variflex
Studies show that about 90% of people's time is spent indoors in North America and Europe. Therefore, it is important to be aware of the health impacts that indoor air quality might have. Low Volatile Organic Compounds (VOCs) are useful indicators of indoor air quality, which is also a factor for building certification systems such as DGNB, LEED, and BREEAM.
In a recent emissions test by the eco-INSTITUT, the Variflex movable wall system by Dorma Hüppe was analyzed for its VOCs content. As a result of the 28-day test, the Variflex product showed only 0.021 mg/m³ VOCs, while the maximum allowed reference value is 1 mg/m³, based on the AgBB (Committee for Health-related Evaluation of Building Products) guidance.
Electrostatic discharges: for various Electronic Access & Data products, we focus on product certification. For example, the dormakaba Wireless Gateway 90 42 is certified according to EN 55024, which tests for immunity in cases of electrostatic discharges, power surges and interruptions, or radio frequency interference. The product is also certified according to IEC 60950, which specifies requirements intended to reduce the risk of fire, electric shock, or injury to the service person, operator, or end user who may come into contact with the product.
Emergency exits and escape routes: automatic doors are subject to the highest safety demands, in accordance with EN 16005. To meet these demands, self-monitoring sensors are mandatory. Obstacle self-detection and automatic reversing are also included in many products. For example, the KTV ATRIUM revolving door systems feature a safety sensor system. Emergency exit and escape route doors are equipped with a redundant operator, an additional control unit for safety purposes, and a self-monitoring motion detector. Additionally, revolving doors require a safety risk assessment before installation, in accordance with DIN 18650. This is provided by us at the building site before a sale is made.
Customer complaint process
In case of emerging risks and customer complaints, we have a Group-wide customer complaint process in place based on the principles of ease of access, solution-driven expertise, short response times, positivity, and focus on our value “Customer First”.
The process follows five steps:
- Acknowledge that the customer has an issue, ideally within 24 hours.
- Assess the problem, prioritize, and find a solution driver.
- Resolve the issue.
- Respond in a timely manner, keeping the customer informed of the status.
- Conclude with a proper follow-up to assess the customer’s satisfaction and integrate lessons learned.
- Regulatory compliance is at the top of the list of priorities for any product development leader and requires immediate action plans. An incident response plan is also put in place to enable direct access to the required resources.
Key & Wall Solutions
Our Key & Wall Solutions business manufactures automotive solutions, keys, and space-dividing solutions. Both our Key Systems and Movable Walls business units have individual approaches to customer health and safety that are product-specific.
The business unit Key Systems approaches customer health and safety as an element of its ISO 9001 certifications and ensures compliance with both mandatory (such as the European CE Declaration of Conformity) and voluntary safety standards. It has over 16 product certifications. Each Key Systems product features: proper documentation, such as a user manual; a Declaration of Compliance; contact details for the manufacturer; quick guides and tutorials available on the web; and training on demand or during product installation to provide the customer with all the information relevant for proper product use and safety features. Regional distributors are periodically trained on the same topics.
In addition to the Group-wide customer complaint process, there is a further grievance mechanism operated by Quality Assurance managers. The management steps involved are: registering the complaint in the ticketing system, evaluation, problem analysis and corrective actions, verification, lessons learned, and closure. The effectiveness of the grievance mechanism is based on the number of open, accepted, refused, and closed complaints per fiscal year. Additionally, at least once a year, a management review assessment evaluates related KPIs and performance status.
Raising awareness about the safe use and installation of our products
Besides certifications and maintaining our high-standard processes, we also believe that it is important to efficiently communicate with our partners and customers about the safe installation, operation, and use of our products. We have set the following targets to further minimize any health and safety risks related to our products. By 2027, we aim to:
- collaborate on health and safety trainings with subcontractors and installation partners;
- collaborate on trainings and provide information materials on the safe operation of our products to all end users; and
- have at least one corrective action and/or one awareness training for each product-related injury.
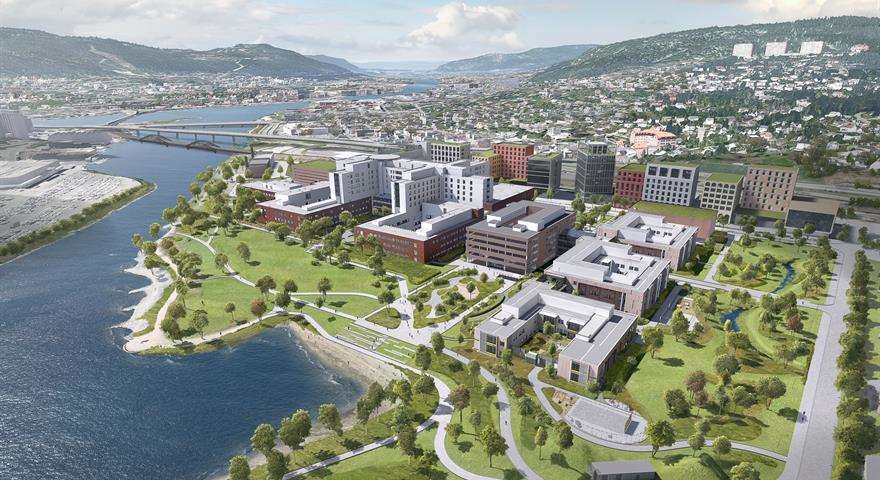
Safety and maintenance training for hospital staff
We are providing door hardware products and special hermetic doors to the new Drammen Hospital in Norway, for example 3800 series levers, ED 250, TS 98 XEA, and mechanical key systems. As part of the product delivery, we have also started developing eLearning modules on the safe use of these doors and interlock solutions, to be shared with all hospital staff. Furthermore, we will deliver on-site trainings on maintenance - related topics to the technical staff and facility managers. The project will be finished in 2025.
Our performance
We internally and externally verify customer health and safety through various certification programs including ISO 9001, testing, and stakeholder feedback. In FY 2021/22, 55% of reporting sites achieved ISO 9001 certification.
55% of our sites have achieved ISO 9001 certification
ESG Performance TableIn FY 2021/22, there have been no incidents of non-compliance with regulations or voluntary codes concerning the health and safety impacts of products and services that have resulted in a fine, penalty, or written warning.
Outlook
We will continue our efforts to ensure customer health and safety in relation to the use of our products. Management of product safety has been very locally driven in the past, making the development of global processes a challenge. In FY 2022/23, a global sufficiency assessment on product safety trainings and information materials is planned to optimize our internal processes.