Materials
10 minKnowing that healthier materials contribute to customer health and safety, we focus on choosing materials that are both safe and enviromentally friendly.
Why it matters
It has been well documented that healthier building materials have a positive impact on building occupants’ well-being. We therefore focus on choosing product materials that are both environmentally friendly and consumer safe to ensure we are simultaneously addressing any impacts to the environment and to our customers’ health and safety.
Read about the low VOC emissions test results for our Variflex 100 room partitioning system
Read storyKey activities
dormakaba products are manufactured around the world using different processes. The most utilized non-renewable raw materials include metals such as steel, brass, aluminum, nickel silver and zinc, as well as gypsum board, glass and plastics. Other important materials are wood, paper and cardboard which are made from renewable resources. Metal parts are often converted, for example, into door closers, cylinders, key blanks, hotel locks and glass fittings. Glass, wood and gypsum board are primarily utilized in sliding and revolving door systems and movable walls.
The potentially greatest environmental risks lie in the processes used for (1) electroplating and surface finishing, (2) painting, (3) melting, and (4) zinc and aluminum die casting. These manufacturing processes are used at 27 of the 73 locations covered in this report. To reduce our environmental footprint, we focus on monitoring and mitigating the environmental impact of these operational steps. When it comes to optimizing our choice of materials, we focus on complying with international material requirements; developing environment- and health-related product declarations; and utilizing the life cycle approach whenever possible. In addition, since the primary extraction of metals from ore and the subsequent refining processes are resource intensive, dormakaba uses metals with recycled content whenever possible. Further, we generally send scrap metal to recycling.
Knowing that healthier materials contribute to customer health and safety, and that architects and building inhabitants wish to have more transparency on the content of products, we highlight the possible health impacts of our products. We have developed various Health Product Declarations (HPDs) and regularly perform tests – for example on volatile organic compounds (VOCs) in a movable wall product or on hazardous substances in electronic products. To reduce our environmental and customer impacts related to the choice of materials, dormakaba focuses on three areas:
- Complying with international material requirements
- Health-related product declarations
- Closing cycles
Complying with international material requirements
We manage compliance issues on both an ad-hoc and strategic basis. Customer and internal requests on training, for example, are addressed ad hoc; while liaising with external legal support is a more strategic endeavor in order to review the requirements and drafting of a Group Directive Material Compliance document.
In the financial year 2018/2019, we were impacted by major changes to the EU Regulation 1907/2006 (REACH). Lead, which is used in a lot of metal alloys, has now been classified as a Substance of Very High Concern (SVHC) by the European Chemicals Agency (ECHA). After assessing the impact of this change, we discussed the use of lead with our suppliers, reviewed our product portfolio and informed our customers, as required by law.
With these regulatory changes, we have implemented material compliance requirements in our enterprise resource planning (ERP) software, with a RoHS label in the Access Solutions (AS) DACH segment. We have discussed several other opportunities to improve transparency on used materials and compliance (in relation to other international material composition restrictions) both internally and with potential service providers. The complexity of our upstream and downstream supply chain and of our products’ bill of materials demonstrates the need for a Group-wide strategic approach, which we plan to further develop over the next few years.
We also made an initial assessment of the possible impacts of the upcoming EU Regulation 2017/821 (Conflict Minerals) during the reporting year. Our assessment is still ongoing and necessary actions will be determined before the regulation comes into effect in January 2021.
Through our Supplier Code of Conduct, we set clear expectations that our suppliers should actively support ongoing efforts to manage and demonstrate product compliance with the above-noted regulations.
Health-related product declarations
dormakaba offers various health-related product declarations which transparently account for the materials found in our products. These are in the form of HPDs, Building Product Declarations (BPDs) or Declare Labels, depending on local market requirements.
An HPD provides a detailed list of the materials and contents of a building product and the associated effects on human health. The declaration is a common reporting format with which the required transparency can be guaranteed.
In the financial year 2018/19, dormakaba updated 19 existing HPDs to the latest version of the standard. Additionally, we updated existing BPDs to the updated standard from the Byggvarubedömningen (BVB), a business association of Sweden’s major property owners and building contractors, which originally developed the standard. The new requirements have become more extensive, which means that the information must be provided in more detail, e.g. information on chemical content and life cycle assessment. BVB now asks for additional documents like Material Compliance Statements or Safety Data Sheets. More than 20 BPDs have been newly updated and published in the financial year 2018/19.
Closing cycles
Several production sites focus on close-loop systems in their material use. Key Systems business unit’s manufacturing facility in Rocky Mount (USA), for example, purchases brass scrap from recyclers to produce its keys. The plant recycles most internal scrap, either back into its own processes or by selling it to a local approved recycler. Scrap material is also sent back to the original producer, who then uses it to make our purchased materials, resulting in a closed-loop system. For the fifth year in a row, the production facility in Vittorio Veneto accomplished this with over 70% of produced scrap going back into its closed-loop system.
The AS AMER manufacturing facility in Indianapolis conducts on-site oil reclamation generated from the machining processes. The site utilizes a system whereby oil is spun off of the scrap metal and collected for re-processing. Once the water content in the oil is evaporated, the oil is reconditioned and supplied back to the equipment for use. Similar to Key Systems in Rocky Mount, the AS AMER facilities use recyclers for all the scrap metal generated during their manufacturing process.
Our performance
dormakaba has made good progress in enhancing our products and their material composition and origin, beyond the legal requirements. This contributes to achieving the dormakaba sustainability target of having EPDs and/or HPDs for products representing 30% of total turnover by the end of financial year 2020/21.
We have continued to improve over the last two years on Material Compliance, but we have more work to do to advance our agenda and performance. We understand that Material Compliance constitutes good governance and we work hard to ensure legal compliance and to create more transparency about the materials we use in our manufacturing processes. We believe that the number of regulations – along with the needs and expectations of our customers regarding healthy materials and products – will rise further. There are many challenges to tackle; for example, material compliance requires the extensive collection of data. Our supply chains are global and complex which makes it difficult to conduct any necessary follow up or investigation. And we have to ensure that changes in material composition do not impact product quality.
For example, over the last year, the Key Systems business unit noticed a general growing interest in our products’ materials, both from our customers and from regulatory authorities (including Customs) worldwide. In fact, we were often required to provide Material Compliance documentation even in countries or regions traditionally less strict in this regard (e.g. Africa, South America, China, Russia). One of the major achievements in the financial year 2018/19 was in meeting the requirements of California Proposition 65, while the biggest challenge was related to the amended RoHS requirements under Directive 2015/863/EC. Key Systems products recently brought to market are in fact RoHS 2015/863/EC compliant, while at the end of the financial year 2018/19 remaining products were on course to meet the compliance deadline.
in metric tons1) |
| 2018/19 |
Non-renewable resources |
| 68,599 |
Steel (incl. stainless steel) |
| 35,997 |
Brass |
| 10,422 |
Aluminium |
| 9,905 |
Nickel silver |
| 2,051 |
Zinc |
| 3,576 |
Copper |
| 8 |
Gypsum Board |
| 2,954 |
Glass |
| 2,389 |
Plastics (parts and packaging material) |
| 1,297 |
Renewable resources |
| 12,109 |
Wood (incl. packaging material) |
| 8,017 |
Paper and cardboard (incl. packaging material) |
| 4,092 |
1)Not included are materials and volumes which can only be accounted for in pieces or monetary terms.
Material use (in %)
Raw material use (in %)
Outlook
An important change will come into effect in July 2019 when, in addition to monitoring and control instruments, all other electrical and electronic equipment will be required to be compliant with EU Directive 2011/65/EU (RoHS) if sold in Europe. At the same time, an additional amendment of four substances in the same Directive will also come into effect. In preparation, we have reviewed all bill of materials for electronic products and performed tests on chosen products to ensure compliance.
To further enhance our HPD offering, the Movable Walls business unit has committed to publishing ten HPDs by March 2020. In addition, five new BPDs are planned for the upcoming financial year.
Spotlight on DORMA Hüppe Variflex 100
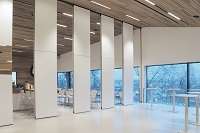
Variflex 100 room partitioning system is proven to have low emissions, healthier for building inhabitants
The Variflex 100 has passed health-related emissions testing for Volatile Organic Compounds (VOCs) with excellent results, showing emissions values far below the allowed levels. Products with low levels of VOCs, such as the Variflex 100, can support the health of building inhabitants.
VOCs are organic chemicals with high vapor pressure, which causes them to easily evaporate into the surrounding air. High concentrations can cause health issues to building users such as headaches, irritation of the mucous membranes and respiratory tract, fatigue, reduced performance or sleep disorders. VOC levels are often looked at in connection with indoor air quality, also by building certification systems such as the DGNB (German Sustainable Building Council) or LEED (Leadership in Energy and Environmental Design).
|
| Total VOC Result |
Variflex 100 |
| 57 µg/m3 |
Maximum allowable level |
| 1,000 µg/m3 |
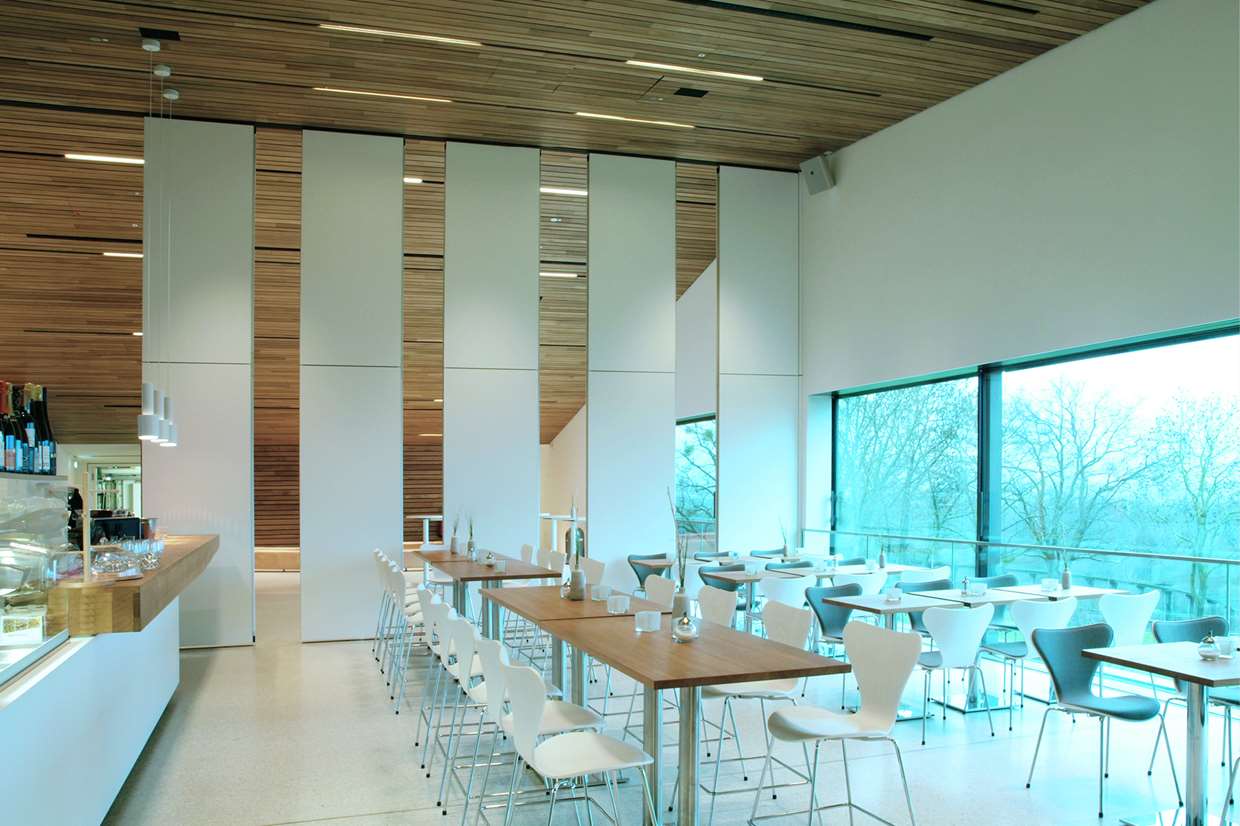