Occupational Health & Safety
9 minThroughout our business and most especially in our manufacturing sites worldwide, the health and safety of our employees is a priority.
Why it matters
The protection of the physical and mental integrity and wellbeing of employees is a core responsibility of dormakaba. Accidents and work-related illnesses can be of a long-term nature and entail costs to society and the company. We can only be successful in the long term if we help ensure our employees remain healthy. Occupational health and safety (OHS) addresses not only the safe operation of machines, ergonomic workplaces or the handling of hazardous substances, but also mental health issues including stress, depression and emotional wellbeing. We strive to simultaneously create optimal working conditions for our employees and to ensure operational efficiencies.
Key activities
Throughout our business and particularly at our manufacturing sites worldwide, the health and safety of our employees is a priority. We want to provide a safe workplace, though many injuries are still occurring in and around our facilities: including cuts, stumbles, commuting accidents, burns in smelting operations, heavy lifting or exposure to toxic fumes in galvanization processes. Currently, dormakaba has only location-specific systems in place to align with national regulations and standards.
Read about the value of ISO 45001 certification from Nassab Khalife, QHES Manager in Dubai.
Read interviewIt is our goal that, by the end of financial year 2021/22, all dormakaba manufacturing sites will maintain an occupational health and safety management system based on the rigorous standards set forth by ISO 45001 or OHSAS 18001. 65% of our manufacturing sites have already achieved this. These sites have designated safety personnel, safety committees, regular safety training, and they collaborate with external partners to ensure that health and safety standards are integrated in prevailing production processes at dormakaba.
In addition, 21% of the manufacturing sites covered in this report benefit from the ISO 45001 or OHSAS 18001 certification. Our facility in Dubai, for example, achieved ISO 45001 certification in the 2018/19 financial year. The table below gives an overview of these indicators for all reporting sites, including offices.
Segment |
| OHSAS 18001 Certificate or similarly certified |
| Maintain OHS Management System |
AS AMER |
|
| 15 | |
AS APAC |
| 1 |
| 5 |
AS DACH |
| 4 |
| 7 |
AS EMEA |
| 8 |
| 13 |
KWS |
| 1 |
| 3 |
Total |
| 14 |
| 43 |
% locations covered in reporting scope* |
| 19% |
| 59% |
% employees covered (versus Group-wide FTEs) |
| 19% |
| 50% |
*Including offices
To ensure our employees remain healthy, dormakaba focuses on three areas:
- Employee engagement and training
- Reducing hazardous materials
- Designated safety personnel and safety committees
Employee engagement and training
To identify and address our health and safety risks, employee engagement is crucial. Our employees are encouraged to report challenges and near misses in order to address these risks. Access Solutions (AS) AMER, for example, regularly trains employees to report near miss incidents that have a potential for injury or property damage in an effort to be proactive. This program helps employees recognize hazards or unsafe acts and to correct them immediately or to ask for support to correct the issue. Near miss reports are treated the same as injury reports, and the respective supervisor follows up with the near miss to ensure it is corrected.
Examples of our employee engagement and training in the financial year 2018/19 included:
- AS AMER has 13 sites that are implementing and maintaining health and safety management systems. Each has set up facility-specific plans and policies and documented them for the internal audit team to evaluate conformance with roll-out plans. AS AMER targeted five Environmental, Health & Safety (EHS) areas of focus for the financial year 2018/19, which included the implementation of the EHS Management System, development of an EHS training program and training matrix, establishment of site EHS Committees, machine guarding improvements and the implementation of an ergonomic program.
- AS DACH in Germany plans to develop and introduce a health management system to improve employee health and reduce the rate of sick leave. The system will be implemented over the next few years. The first initiative to date has been an information campaign on colds and flu.
- AS APAC in Suzhou (China) has filmed two safety videos, one for employees and the other for visitors and contractors. All employees are required to watch the video on their first day of work, while visitors and contractors will watch it upon arrival at the facility.
Reducing hazardous materials
The potential impact on employees’ health of working with hazardous materials is of special concern. Hazardous materials are used as cooling lubricants, oils in machining and for the cutting of raw materials. As well, in the electroplating area some hazardous materials are used to protect materials from corrosion. Our Access Solutions (AS) DACH segment therefore systematically carries out hazardous material substitutions and tracks reductions in hazardous material usage.
In the last four financial years, hazardous materials have been reduced by 80%.
Hazard Symbol |
| FY 2015/16 |
| FY 2016/17 |
| FY 2017/18 |
| FY 2018/19 |
| Change vs. FY 2015/16 |
(T+) Very toxic |
| – |
| – |
| – |
| – |
| n/a |
(T) Toxic |
| 5 |
| 4 |
| 2 |
| 3 |
| –40% |
(C) Corrosive |
| 24 |
| 12 |
| 7 |
| 6 |
| –75% |
(Xn) Harmful |
| 64 |
| 40 |
| 26 |
| 9 |
| –86% |
(Xi) Irritant |
| 137 |
| 99 |
| 59 |
| 31 |
| –77% |
(E) Explosive |
| – |
| – |
| – |
| – |
| n/a |
(F+) Extremely flammable |
| 46 |
| 21 |
| 12 |
| 6 |
| –87% |
(F) Highly flammable |
| 32 |
| 24 |
| 15 |
| 9 |
| –72% |
(O) Oxidizing |
| 4 |
| 1 |
| 1 |
| 1 |
| –75% |
(U) Dangerous for the environment |
| 45 |
| 30 |
| 13 |
| 9 |
| –80% |
No hazard symbol |
| 262 |
| 264 |
| 320 |
| 351 |
| 34% |
Examples of our activities to reduce hazardous materials in the financial year 2018/19 included:
- AS AMER has implemented a new segment-wide service to house and update all chemical Safety Data Sheets for each site. This new web-based system allows facilities to easily analyze the current hazardous materials in order to prioritize for material substitution. For instance, the Indianapolis facility recently eliminated the use of a product containing n-Propyl Bromide for cleaning metal parts.
- Additionally, the Key Systems business unit’s manufacturing facility in Rocky Mount (USA) has secondary containment areas and sumps which flow to wastewater treatment, tank secondary self-containment, safety barrier curtains and emergency showers and eyewash stations.
- AS APAC in Singapore made a substantial investment in a new painting system in order to switch over from solvent-based to water-based application last year. This change is estimated to have reduced solvent consumption by 38% per month.
Designated safety personnel and safety committees
dormakaba employs designated safety personnel and safety committees in order to ensure that workers comply with company policies and government regulations. These forums also facilitate communication and cooperation between management and personnel.
Examples of our safety personnel and safety committee activities in the financial year 2018/19 include:
- The Key Systems business unit’s manufacturing facility in Rocky Mount (USA) has a designated EHS manager who is responsible for monitoring workplace activities, developing programs and providing safety training. The manager is also responsible for assessing hazardous and unsafe situations and developing measures to assure personnel safety. The plant maintains a safety committee. Its aim is to reduce incidences of injury and illnesses through: education and discussion; openly communicating with employees on safety matters; building enthusiasm for health and safety initiatives; and by making health and safety activities, such as hazard identification, an integral part of its operating procedures, culture and programs.
- Similarly, AS DACH has dedicated safety personnel who also ensure that, among other duties, accidents are analyzed with a so-called STOP (Substitution, Technical, Organizational, Personnel) system: i.e. for each accident, a report is developed, including photographic evidence, and a process is implemented to eliminate or reduce the likelihood of further incidence. Also, a point system is in place: points are allocated to actions that lead to the successful elimination of the injury risk.
- Each AS AMER manufacturing site has established an EHS Committee comprised of various employees from different departments and shifts. These committees have each developed a written procedure and vision statement, and they hold regular meetings to establish goals and action plans. Committee activities are communicated to all employees and committee members receive advanced EHS training on relevant topics.
Our performance
Of our reporting sites, 19% had a health and safety management system certified to OHSAS 18001, ISO 45001 or the equivalent local standard; and 59% maintain a health and safety management system. For these sites, health and safety training goes beyond the mandatory requirements to include emergency and risk prevention. For example, assessments of repetitive movement and heavy load-lifting, to prevent work-related illnesses, take place at various sites.
In the financial year 2018/19, 259 occupational injury cases were registered (2.1 per 100 full-time employees), compared to 260 in the previous reporting year. Regionally, occupational injury cases were reported as follows: 7 in Switzerland (1.4), 58 in Germany (2.1), 63 in the rest of Europe, Middle East and Africa (2.3), 75 (2.5) in the Americas, and 56 (1.7) in Asia-Pacific. There were no fatalities as a result of work-related injuries in the financial year 2018/19.
Access Solutions (AS) AMER recorded a 29% decrease in employee injuries in the financial year 2018/19 compared to the previous year. The segment also experienced a 40% decrease in more severe injuries, i.e. injuries that result in time away from work or light-duty restrictions. Each manufacturing site in the AS AMER segment has addressed the five EHS Emphasis Topics, providing a framework for many safety improvements. These include upgrades to machine guarding, facility shipping dock upgrades, completion of ergonomic assessments and personal protective equipment evaluations. Future plans include additional EHS Emphasis Topics for the coming fiscal year, standardization of safety signage and factory floor markings, and enhanced EHS training for managers and supervisors.
Outlook
We continue our efforts to ensure our employees remain safe and healthy. For instance, we are rolling out a Health and Safety Committee in Victoria (Australia), which will incorporate representatives from technical, operations and office staff. The Middle East & Africa region will also roll out a corporate wellness program with on-site classes and courses that target better mental and physical health including stress management, weight management and healthy eating, work life balance, and smoking cessation. Additionally, our manufacturing facility in Suzhou (China) is working on a project to switch over its painting system from solvent-based painting to water-based painting in the financial year 2018/19 and expects to complete it by the financial year 2020/21.
The value of ISO 45001 certification
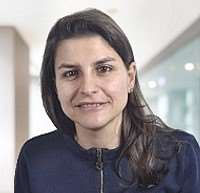
An interview with Nasab Khalife, dormakaba Quality, Health, Safety and Environment Manager, United Arab Emirates
In October 2018, our site in Dubai was recommended for ISO 45001 for its health and safety management. Why did you choose to get certified?
We already had some processes and initiatives in place related to health & safety, and we wanted to put all of these actions into a single, organized framework. That is why we opted for ISO 45001. Also, having ISO certifications for quality, environment, and health and safety are becoming, more and more, a fundamental requirement for new projects and tenders in Dubai.
What were the biggest challenges in the certification process? And how did you address these?
Our main issue was managing the shop floor space, as we have a limited area. At the same time, we were all convinced that organizing the area was fundamental not only for certification, but for our own safety and the safety of our employees. The certification was an extra push and it helped us to speed up this project. With the help of our operations and production team, we were able to overcome this challenge.
What value do you see in the ISO 45001 certification?
Certification is a confirmation that our system is working properly in regard to health and safety. Also, it gives us an advantage among our competitors, because we have been early adopters of the recently released ISO 45001 standard.